What is the Mainstream Ceramic Capacitor Production Process?
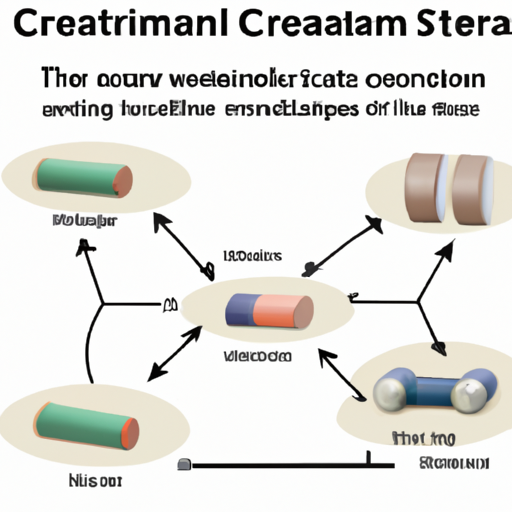
I. Introduction
Ceramic capacitors are essential components in modern electronic devices, playing a crucial role in energy storage, filtering, and signal coupling. These capacitors are favored for their stability, reliability, and ability to operate over a wide range of temperatures and voltages. As the demand for smaller, more efficient electronic devices continues to rise, understanding the production process of ceramic capacitors becomes increasingly important. This blog post will explore the mainstream ceramic capacitor production process, from raw materials to future trends in the industry.
II. Types of Ceramic Capacitors
Ceramic capacitors are categorized into two main classes based on their dielectric properties: Class 1 and Class 2 capacitors.
A. Class 1 Capacitors
Class 1 capacitors, such as C0G and NP0, are known for their excellent stability and low loss characteristics. They are typically used in applications requiring precise capacitance values, such as timing circuits and RF applications. The dielectric materials used in Class 1 capacitors are usually temperature-stable and exhibit minimal capacitance change over varying temperatures.
B. Class 2 Capacitors
Class 2 capacitors, including X7R and Y5V, are designed for applications where higher capacitance values are needed, but stability is less critical. These capacitors can exhibit significant capacitance variation with temperature and voltage, making them suitable for decoupling and filtering applications in power electronics. The dielectric materials used in Class 2 capacitors, such as barium titanate, allow for higher capacitance in a smaller package.
C. Differences in Materials and Applications
The choice between Class 1 and Class 2 capacitors depends on the specific requirements of the application. Class 1 capacitors are preferred for precision applications, while Class 2 capacitors are often used in consumer electronics where size and cost are more critical than absolute stability.
III. Raw Materials
The production of ceramic capacitors begins with the selection of high-quality raw materials.
A. Overview of Materials Used
1. **Dielectric Materials**: The most common dielectric material used in ceramic capacitors is barium titanate (BaTiO3). This material exhibits excellent dielectric properties, making it ideal for energy storage. Other materials may include strontium titanate and lead zirconate titanate, depending on the desired characteristics of the capacitor.
2. **Electrode Materials**: The electrodes of ceramic capacitors are typically made from conductive materials such as silver or nickel. Silver is often used for high-performance capacitors due to its superior conductivity, while nickel is more cost-effective for lower-end applications.
B. Quality Control of Raw Materials
Ensuring the quality of raw materials is critical in the production of ceramic capacitors. Manufacturers conduct rigorous testing and analysis to verify the purity and consistency of dielectric and electrode materials. This quality control helps to minimize defects and ensure the reliability of the final product.
C. Sourcing and Environmental Considerations
Sourcing raw materials responsibly is increasingly important in the electronics industry. Manufacturers are focusing on sustainable practices, such as using recycled materials and minimizing waste during production. Additionally, compliance with environmental regulations is essential to reduce the ecological impact of capacitor production.
IV. The Production Process
The production of ceramic capacitors involves several key steps, each contributing to the final product's performance and reliability.
A. Preparation of the Dielectric Material
1. **Mixing and Milling**: The first step in preparing the dielectric material involves mixing the raw materials, including barium titanate, with additives to enhance performance. This mixture is then milled to achieve a fine powder, ensuring uniformity in the dielectric properties.
2. **Calcination**: The milled powder is subjected to calcination, a process that involves heating the material to high temperatures to promote chemical reactions and remove impurities. This step is crucial for achieving the desired dielectric properties.
B. Formation of Ceramic Layers
1. **Tape Casting**: Once the dielectric material is prepared, it is formed into thin ceramic layers using a process called tape casting. In this process, the dielectric slurry is spread onto a flat surface and then dried to create flexible ceramic sheets.
2. **Drying**: The dried ceramic sheets are cut into the desired dimensions for capacitor assembly. Proper drying is essential to prevent cracking and ensure uniform thickness.
C. Electrode Application
1. **Screen Printing**: The next step involves applying electrodes to the ceramic layers. This is typically done using screen printing, where a conductive paste (usually containing silver or nickel) is printed onto the ceramic layers.
2. **Sintering**: After the electrodes are applied, the assembled layers undergo sintering, a process that involves heating the components to a temperature where the particles bond together without melting. This step is critical for achieving the desired electrical and mechanical properties.
D. Assembly of Capacitor Components
1. **Layer Stacking**: The ceramic layers with electrodes are stacked together to form the capacitor structure. The number of layers can vary depending on the desired capacitance value.
2. **Pressing**: The stacked layers are then pressed to ensure proper alignment and contact between the layers. This step helps to eliminate air pockets and improve the overall performance of the capacitor.
E. Final Sintering Process
1. **Temperature and Atmosphere Control**: The final sintering process is conducted in a controlled environment, where temperature and atmosphere are carefully regulated. This ensures that the dielectric properties are optimized and that the electrodes bond effectively to the ceramic layers.
2. **Effects on Dielectric Properties**: The final sintering process significantly influences the dielectric properties of the capacitor, including capacitance, dissipation factor, and temperature stability. Manufacturers must carefully monitor this step to achieve the desired performance characteristics.
V. Testing and Quality Control
Once the ceramic capacitors are produced, they undergo rigorous testing to ensure they meet industry standards and customer specifications.
A. Electrical Testing
1. **Capacitance Measurement**: Each capacitor is tested for its capacitance value to ensure it falls within the specified range. This measurement is critical for ensuring the capacitor's performance in its intended application.
2. **Voltage Rating Tests**: Capacitors are subjected to voltage rating tests to verify their ability to withstand specified voltage levels without failure. This testing helps to ensure reliability in real-world applications.
B. Mechanical Testing
1. **Physical Integrity Checks**: Capacitors are inspected for physical defects, such as cracks or misalignments, which could affect performance. This step is essential for ensuring the mechanical integrity of the components.
2. **Thermal Cycling Tests**: Capacitors are subjected to thermal cycling tests to evaluate their performance under varying temperature conditions. This testing helps to identify potential failures due to thermal stress.
C. Compliance with Industry Standards
Manufacturers must ensure that their ceramic capacitors comply with industry standards, such as ISO and IEC. Compliance with these standards is essential for ensuring product quality and reliability.
VI. Packaging and Distribution
Once the ceramic capacitors have passed testing, they are packaged and prepared for distribution.
A. Types of Packaging for Ceramic Capacitors
Ceramic capacitors are typically packaged in anti-static materials to protect them from electrostatic discharge (ESD) during transportation. Common packaging methods include bulk packaging, tape and reel, and tray packaging, depending on the intended application.
B. Importance of Packaging in Protecting Components
Proper packaging is crucial for protecting ceramic capacitors from physical damage and environmental factors during shipping and storage. Manufacturers must ensure that their packaging solutions are robust and effective in safeguarding the components.
C. Distribution Channels and Logistics
The distribution of ceramic capacitors involves various channels, including direct sales, distributors, and online platforms. Efficient logistics are essential for ensuring timely delivery to customers and maintaining a competitive edge in the market.
VII. Challenges in Production
The production of ceramic capacitors is not without its challenges.
A. Variability in Material Properties
Variability in the properties of raw materials can lead to inconsistencies in the final product. Manufacturers must implement strict quality control measures to minimize these variations and ensure uniformity in performance.
B. Environmental Regulations and Sustainability
As environmental regulations become more stringent, manufacturers face challenges in sourcing materials and managing waste. Embracing sustainable practices and developing eco-friendly materials are essential for meeting these regulations.
C. Technological Advancements and Automation
The rapid pace of technological advancements presents both opportunities and challenges for ceramic capacitor production. Manufacturers must continuously invest in automation and innovative processes to remain competitive in the market.
VIII. Future Trends in Ceramic Capacitor Production
The future of ceramic capacitor production is shaped by several key trends.
A. Innovations in Materials and Processes
Research and development efforts are focused on discovering new dielectric materials and production processes that enhance performance and reduce costs. Innovations in materials science may lead to the development of capacitors with improved characteristics.
B. The Impact of Miniaturization on Production
As electronic devices continue to shrink in size, the demand for smaller ceramic capacitors is increasing. Manufacturers must adapt their production processes to accommodate these changes while maintaining performance and reliability.
C. Market Demand and Growth Projections
The global market for ceramic capacitors is expected to grow significantly in the coming years, driven by the increasing demand for consumer electronics, automotive applications, and renewable energy technologies. Manufacturers must be prepared to meet this growing demand through efficient production and innovative solutions.
IX. Conclusion
In conclusion, the production process of ceramic capacitors is a complex and multifaceted endeavor that requires careful attention to detail at every stage. From the selection of raw materials to the final testing and packaging, each step plays a critical role in ensuring the quality and reliability of the final product. As the electronics industry continues to evolve, the importance of innovation and sustainability in ceramic capacitor production will only grow. By embracing new technologies and practices, manufacturers can position themselves for success in a rapidly changing market, ensuring that ceramic capacitors remain a vital component in the future of electronics.
What is the Mainstream Ceramic Capacitor Production Process?
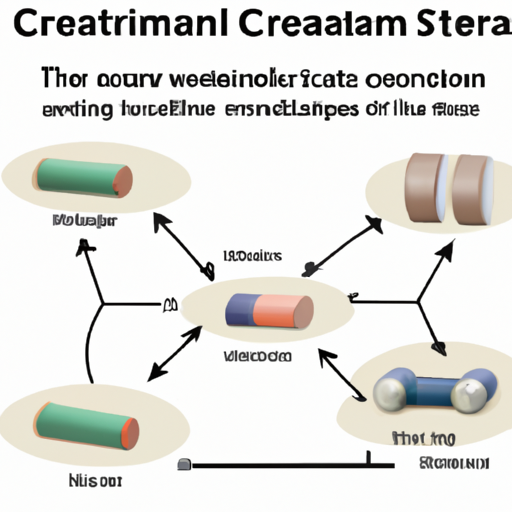
I. Introduction
Ceramic capacitors are essential components in modern electronic devices, playing a crucial role in energy storage, filtering, and signal coupling. These capacitors are favored for their stability, reliability, and ability to operate over a wide range of temperatures and voltages. As the demand for smaller, more efficient electronic devices continues to rise, understanding the production process of ceramic capacitors becomes increasingly important. This blog post will explore the mainstream ceramic capacitor production process, from raw materials to future trends in the industry.
II. Types of Ceramic Capacitors
Ceramic capacitors are categorized into two main classes based on their dielectric properties: Class 1 and Class 2 capacitors.
A. Class 1 Capacitors
Class 1 capacitors, such as C0G and NP0, are known for their excellent stability and low loss characteristics. They are typically used in applications requiring precise capacitance values, such as timing circuits and RF applications. The dielectric materials used in Class 1 capacitors are usually temperature-stable and exhibit minimal capacitance change over varying temperatures.
B. Class 2 Capacitors
Class 2 capacitors, including X7R and Y5V, are designed for applications where higher capacitance values are needed, but stability is less critical. These capacitors can exhibit significant capacitance variation with temperature and voltage, making them suitable for decoupling and filtering applications in power electronics. The dielectric materials used in Class 2 capacitors, such as barium titanate, allow for higher capacitance in a smaller package.
C. Differences in Materials and Applications
The choice between Class 1 and Class 2 capacitors depends on the specific requirements of the application. Class 1 capacitors are preferred for precision applications, while Class 2 capacitors are often used in consumer electronics where size and cost are more critical than absolute stability.
III. Raw Materials
The production of ceramic capacitors begins with the selection of high-quality raw materials.
A. Overview of Materials Used
1. **Dielectric Materials**: The most common dielectric material used in ceramic capacitors is barium titanate (BaTiO3). This material exhibits excellent dielectric properties, making it ideal for energy storage. Other materials may include strontium titanate and lead zirconate titanate, depending on the desired characteristics of the capacitor.
2. **Electrode Materials**: The electrodes of ceramic capacitors are typically made from conductive materials such as silver or nickel. Silver is often used for high-performance capacitors due to its superior conductivity, while nickel is more cost-effective for lower-end applications.
B. Quality Control of Raw Materials
Ensuring the quality of raw materials is critical in the production of ceramic capacitors. Manufacturers conduct rigorous testing and analysis to verify the purity and consistency of dielectric and electrode materials. This quality control helps to minimize defects and ensure the reliability of the final product.
C. Sourcing and Environmental Considerations
Sourcing raw materials responsibly is increasingly important in the electronics industry. Manufacturers are focusing on sustainable practices, such as using recycled materials and minimizing waste during production. Additionally, compliance with environmental regulations is essential to reduce the ecological impact of capacitor production.
IV. The Production Process
The production of ceramic capacitors involves several key steps, each contributing to the final product's performance and reliability.
A. Preparation of the Dielectric Material
1. **Mixing and Milling**: The first step in preparing the dielectric material involves mixing the raw materials, including barium titanate, with additives to enhance performance. This mixture is then milled to achieve a fine powder, ensuring uniformity in the dielectric properties.
2. **Calcination**: The milled powder is subjected to calcination, a process that involves heating the material to high temperatures to promote chemical reactions and remove impurities. This step is crucial for achieving the desired dielectric properties.
B. Formation of Ceramic Layers
1. **Tape Casting**: Once the dielectric material is prepared, it is formed into thin ceramic layers using a process called tape casting. In this process, the dielectric slurry is spread onto a flat surface and then dried to create flexible ceramic sheets.
2. **Drying**: The dried ceramic sheets are cut into the desired dimensions for capacitor assembly. Proper drying is essential to prevent cracking and ensure uniform thickness.
C. Electrode Application
1. **Screen Printing**: The next step involves applying electrodes to the ceramic layers. This is typically done using screen printing, where a conductive paste (usually containing silver or nickel) is printed onto the ceramic layers.
2. **Sintering**: After the electrodes are applied, the assembled layers undergo sintering, a process that involves heating the components to a temperature where the particles bond together without melting. This step is critical for achieving the desired electrical and mechanical properties.
D. Assembly of Capacitor Components
1. **Layer Stacking**: The ceramic layers with electrodes are stacked together to form the capacitor structure. The number of layers can vary depending on the desired capacitance value.
2. **Pressing**: The stacked layers are then pressed to ensure proper alignment and contact between the layers. This step helps to eliminate air pockets and improve the overall performance of the capacitor.
E. Final Sintering Process
1. **Temperature and Atmosphere Control**: The final sintering process is conducted in a controlled environment, where temperature and atmosphere are carefully regulated. This ensures that the dielectric properties are optimized and that the electrodes bond effectively to the ceramic layers.
2. **Effects on Dielectric Properties**: The final sintering process significantly influences the dielectric properties of the capacitor, including capacitance, dissipation factor, and temperature stability. Manufacturers must carefully monitor this step to achieve the desired performance characteristics.
V. Testing and Quality Control
Once the ceramic capacitors are produced, they undergo rigorous testing to ensure they meet industry standards and customer specifications.
A. Electrical Testing
1. **Capacitance Measurement**: Each capacitor is tested for its capacitance value to ensure it falls within the specified range. This measurement is critical for ensuring the capacitor's performance in its intended application.
2. **Voltage Rating Tests**: Capacitors are subjected to voltage rating tests to verify their ability to withstand specified voltage levels without failure. This testing helps to ensure reliability in real-world applications.
B. Mechanical Testing
1. **Physical Integrity Checks**: Capacitors are inspected for physical defects, such as cracks or misalignments, which could affect performance. This step is essential for ensuring the mechanical integrity of the components.
2. **Thermal Cycling Tests**: Capacitors are subjected to thermal cycling tests to evaluate their performance under varying temperature conditions. This testing helps to identify potential failures due to thermal stress.
C. Compliance with Industry Standards
Manufacturers must ensure that their ceramic capacitors comply with industry standards, such as ISO and IEC. Compliance with these standards is essential for ensuring product quality and reliability.
VI. Packaging and Distribution
Once the ceramic capacitors have passed testing, they are packaged and prepared for distribution.
A. Types of Packaging for Ceramic Capacitors
Ceramic capacitors are typically packaged in anti-static materials to protect them from electrostatic discharge (ESD) during transportation. Common packaging methods include bulk packaging, tape and reel, and tray packaging, depending on the intended application.
B. Importance of Packaging in Protecting Components
Proper packaging is crucial for protecting ceramic capacitors from physical damage and environmental factors during shipping and storage. Manufacturers must ensure that their packaging solutions are robust and effective in safeguarding the components.
C. Distribution Channels and Logistics
The distribution of ceramic capacitors involves various channels, including direct sales, distributors, and online platforms. Efficient logistics are essential for ensuring timely delivery to customers and maintaining a competitive edge in the market.
VII. Challenges in Production
The production of ceramic capacitors is not without its challenges.
A. Variability in Material Properties
Variability in the properties of raw materials can lead to inconsistencies in the final product. Manufacturers must implement strict quality control measures to minimize these variations and ensure uniformity in performance.
B. Environmental Regulations and Sustainability
As environmental regulations become more stringent, manufacturers face challenges in sourcing materials and managing waste. Embracing sustainable practices and developing eco-friendly materials are essential for meeting these regulations.
C. Technological Advancements and Automation
The rapid pace of technological advancements presents both opportunities and challenges for ceramic capacitor production. Manufacturers must continuously invest in automation and innovative processes to remain competitive in the market.
VIII. Future Trends in Ceramic Capacitor Production
The future of ceramic capacitor production is shaped by several key trends.
A. Innovations in Materials and Processes
Research and development efforts are focused on discovering new dielectric materials and production processes that enhance performance and reduce costs. Innovations in materials science may lead to the development of capacitors with improved characteristics.
B. The Impact of Miniaturization on Production
As electronic devices continue to shrink in size, the demand for smaller ceramic capacitors is increasing. Manufacturers must adapt their production processes to accommodate these changes while maintaining performance and reliability.
C. Market Demand and Growth Projections
The global market for ceramic capacitors is expected to grow significantly in the coming years, driven by the increasing demand for consumer electronics, automotive applications, and renewable energy technologies. Manufacturers must be prepared to meet this growing demand through efficient production and innovative solutions.
IX. Conclusion
In conclusion, the production process of ceramic capacitors is a complex and multifaceted endeavor that requires careful attention to detail at every stage. From the selection of raw materials to the final testing and packaging, each step plays a critical role in ensuring the quality and reliability of the final product. As the electronics industry continues to evolve, the importance of innovation and sustainability in ceramic capacitor production will only grow. By embracing new technologies and practices, manufacturers can position themselves for success in a rapidly changing market, ensuring that ceramic capacitors remain a vital component in the future of electronics.