What are the Latest Manufacturing Processes for Capacitor Charging?
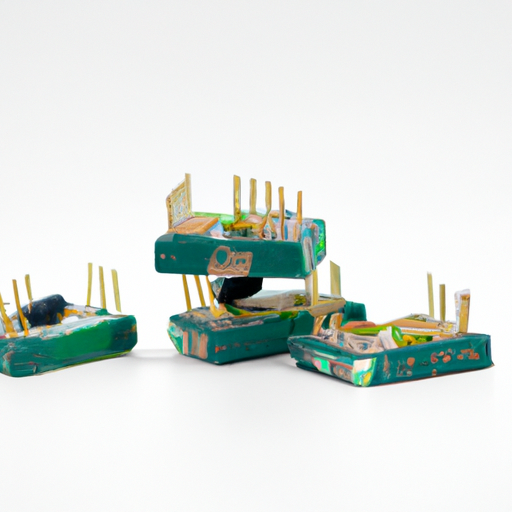
I. Introduction
Capacitors are fundamental components in electronic circuits, serving as energy storage devices that play a crucial role in various applications, from power supply systems to signal processing. Their ability to store and release electrical energy makes them indispensable in modern electronics. The process of charging a capacitor is vital, as it determines how quickly and efficiently the capacitor can store energy for later use. This article aims to explore the latest manufacturing processes for capacitor charging, highlighting advancements that enhance efficiency, precision, and sustainability.
II. Understanding Capacitor Charging
A. Basic Principles of Capacitor Charging
At the core of capacitor charging lies the relationship between voltage, current, and capacitance. When a voltage is applied across a capacitor, it begins to store electrical energy, which is quantified by its capacitance. The charging process involves a current flowing into the capacitor until it reaches the applied voltage, at which point the charging cycle is complete. The time it takes to charge a capacitor is influenced by its capacitance and the resistance in the circuit, leading to distinct charging and discharging cycles.
B. Types of Capacitors and Their Charging Requirements
Different types of capacitors have unique charging requirements:
1. **Electrolytic Capacitors**: Known for their high capacitance values, these capacitors require careful charging to avoid damage due to reverse polarity.
2. **Ceramic Capacitors**: These capacitors are stable and can handle rapid charging and discharging, making them suitable for high-frequency applications.
3. **Film Capacitors**: With excellent stability and low losses, film capacitors are often used in audio and power applications, requiring moderate charging rates.
4. **Supercapacitors**: These devices can charge and discharge rapidly, making them ideal for applications requiring quick bursts of energy, such as in regenerative braking systems.
III. Traditional Manufacturing Processes for Capacitor Charging
A. Overview of Conventional Methods
Historically, capacitor manufacturing involved manual assembly and basic automated systems. Workers would assemble components, test the capacitors, and ensure they met specifications. While this method allowed for quality control, it was time-consuming and labor-intensive.
B. Limitations of Traditional Processes
Traditional manufacturing processes have several limitations:
1. **Time Consumption**: Manual assembly and testing can lead to longer production times, affecting overall efficiency.
2. **Inconsistencies in Quality**: Human error can result in variations in product quality, leading to potential failures in applications.
3. **Safety Concerns**: Handling high-voltage components poses safety risks for workers, necessitating stringent safety protocols.
IV. Advances in Manufacturing Technologies
A. Automation and Robotics
The integration of automation and robotics in capacitor manufacturing has revolutionized the industry. Robotics play a significant role in the assembly and charging processes, allowing for precise placement of components and consistent charging cycles. Automated systems enhance efficiency by reducing production times and minimizing human error, leading to higher quality products.
B. Smart Manufacturing and Industry 4.0
The advent of Industry 4.0 has brought about a new era in manufacturing, characterized by the integration of the Internet of Things (IoT) in capacitor production. Smart manufacturing systems enable real-time monitoring of the manufacturing process, allowing for data analytics to optimize production efficiency. This connectivity facilitates predictive maintenance, reducing downtime and ensuring consistent quality in capacitor charging.
C. Advanced Materials and Techniques
Recent advancements in materials science have led to the development of new dielectric materials that enhance capacitor performance. Innovations in electrode design and fabrication techniques have also improved energy density and charging rates. These advancements allow manufacturers to produce capacitors that are not only more efficient but also more compact, catering to the demands of modern electronic devices.
V. Latest Charging Techniques
A. Fast Charging Technologies
Fast charging technologies have gained prominence, particularly in applications such as electric vehicles (EVs) and renewable energy systems. These methods enable capacitors to charge rapidly, significantly reducing downtime. Techniques such as pulse charging and high-frequency charging are being explored to enhance the speed and efficiency of the charging process.
B. Wireless Charging Solutions
Wireless charging is another innovative approach that is transforming capacitor charging processes. Utilizing principles of electromagnetic induction, wireless energy transfer allows capacitors to charge without direct physical connections. This technology is particularly beneficial in applications where traditional charging methods are impractical, such as in medical devices and consumer electronics.
C. Energy Harvesting Techniques
Energy harvesting techniques focus on capturing ambient energy to charge capacitors, making them ideal for low-power devices. By harnessing energy from sources such as solar, thermal, or kinetic energy, these methods enable capacitors to charge sustainably, reducing reliance on traditional power sources. This approach is particularly valuable in remote or off-grid applications.
VI. Quality Control and Testing in Manufacturing
A. Importance of Quality Assurance in Capacitor Charging
Quality assurance is paramount in capacitor manufacturing, as even minor defects can lead to significant failures in electronic systems. Ensuring that capacitors meet stringent quality standards is essential for maintaining reliability and performance.
B. Latest Testing Methodologies
Recent advancements in testing methodologies have improved the quality control process:
1. **Automated Testing Systems**: These systems allow for rapid and accurate testing of capacitors, ensuring they meet specifications before leaving the production line.
2. **Non-Destructive Testing Techniques**: Methods such as X-ray imaging and ultrasonic testing enable manufacturers to assess the integrity of capacitors without damaging them, providing valuable insights into potential defects.
C. Compliance with Industry Standards and Regulations
Manufacturers must adhere to industry standards and regulations to ensure the safety and reliability of their products. Compliance with standards such as IEC, UL, and RoHS is essential for gaining market acceptance and ensuring consumer trust.
VII. Future Trends in Capacitor Charging Manufacturing
A. Predictions for the Next Decade
The next decade is expected to witness significant advancements in capacitor charging manufacturing. As technology continues to evolve, manufacturers will likely adopt more sophisticated automation and smart manufacturing techniques, further enhancing efficiency and quality.
B. Potential Impact of Emerging Technologies
Emerging technologies such as artificial intelligence (AI) and machine learning are poised to revolutionize capacitor manufacturing. These technologies can optimize production processes, predict maintenance needs, and enhance quality control, leading to more efficient and reliable capacitor charging.
C. Sustainability and Eco-Friendly Practices
Sustainability is becoming increasingly important in manufacturing. Capacitor manufacturers are exploring eco-friendly practices, such as using recyclable materials and reducing energy consumption during production. These efforts not only benefit the environment but also align with consumer demand for sustainable products.
VIII. Conclusion
In conclusion, the landscape of capacitor charging manufacturing is evolving rapidly, driven by advancements in technology and a growing emphasis on quality and sustainability. From automation and smart manufacturing to innovative charging techniques, the industry is poised for significant growth and improvement. As we look to the future, continued research and development will be essential in enhancing the efficiency and performance of capacitor charging processes, ensuring that capacitors remain a vital component in the ever-evolving world of electronics.
IX. References
A comprehensive list of academic papers, industry reports, and relevant literature on capacitor charging and manufacturing processes would be included here to support the information presented in the article.
---
This blog post provides a detailed overview of the latest manufacturing processes for capacitor charging, highlighting the importance of innovation and quality in the industry.
What are the Latest Manufacturing Processes for Capacitor Charging?
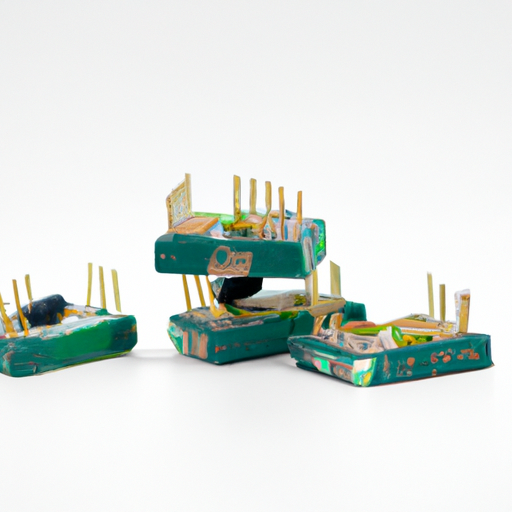
I. Introduction
Capacitors are fundamental components in electronic circuits, serving as energy storage devices that play a crucial role in various applications, from power supply systems to signal processing. Their ability to store and release electrical energy makes them indispensable in modern electronics. The process of charging a capacitor is vital, as it determines how quickly and efficiently the capacitor can store energy for later use. This article aims to explore the latest manufacturing processes for capacitor charging, highlighting advancements that enhance efficiency, precision, and sustainability.
II. Understanding Capacitor Charging
A. Basic Principles of Capacitor Charging
At the core of capacitor charging lies the relationship between voltage, current, and capacitance. When a voltage is applied across a capacitor, it begins to store electrical energy, which is quantified by its capacitance. The charging process involves a current flowing into the capacitor until it reaches the applied voltage, at which point the charging cycle is complete. The time it takes to charge a capacitor is influenced by its capacitance and the resistance in the circuit, leading to distinct charging and discharging cycles.
B. Types of Capacitors and Their Charging Requirements
Different types of capacitors have unique charging requirements:
1. **Electrolytic Capacitors**: Known for their high capacitance values, these capacitors require careful charging to avoid damage due to reverse polarity.
2. **Ceramic Capacitors**: These capacitors are stable and can handle rapid charging and discharging, making them suitable for high-frequency applications.
3. **Film Capacitors**: With excellent stability and low losses, film capacitors are often used in audio and power applications, requiring moderate charging rates.
4. **Supercapacitors**: These devices can charge and discharge rapidly, making them ideal for applications requiring quick bursts of energy, such as in regenerative braking systems.
III. Traditional Manufacturing Processes for Capacitor Charging
A. Overview of Conventional Methods
Historically, capacitor manufacturing involved manual assembly and basic automated systems. Workers would assemble components, test the capacitors, and ensure they met specifications. While this method allowed for quality control, it was time-consuming and labor-intensive.
B. Limitations of Traditional Processes
Traditional manufacturing processes have several limitations:
1. **Time Consumption**: Manual assembly and testing can lead to longer production times, affecting overall efficiency.
2. **Inconsistencies in Quality**: Human error can result in variations in product quality, leading to potential failures in applications.
3. **Safety Concerns**: Handling high-voltage components poses safety risks for workers, necessitating stringent safety protocols.
IV. Advances in Manufacturing Technologies
A. Automation and Robotics
The integration of automation and robotics in capacitor manufacturing has revolutionized the industry. Robotics play a significant role in the assembly and charging processes, allowing for precise placement of components and consistent charging cycles. Automated systems enhance efficiency by reducing production times and minimizing human error, leading to higher quality products.
B. Smart Manufacturing and Industry 4.0
The advent of Industry 4.0 has brought about a new era in manufacturing, characterized by the integration of the Internet of Things (IoT) in capacitor production. Smart manufacturing systems enable real-time monitoring of the manufacturing process, allowing for data analytics to optimize production efficiency. This connectivity facilitates predictive maintenance, reducing downtime and ensuring consistent quality in capacitor charging.
C. Advanced Materials and Techniques
Recent advancements in materials science have led to the development of new dielectric materials that enhance capacitor performance. Innovations in electrode design and fabrication techniques have also improved energy density and charging rates. These advancements allow manufacturers to produce capacitors that are not only more efficient but also more compact, catering to the demands of modern electronic devices.
V. Latest Charging Techniques
A. Fast Charging Technologies
Fast charging technologies have gained prominence, particularly in applications such as electric vehicles (EVs) and renewable energy systems. These methods enable capacitors to charge rapidly, significantly reducing downtime. Techniques such as pulse charging and high-frequency charging are being explored to enhance the speed and efficiency of the charging process.
B. Wireless Charging Solutions
Wireless charging is another innovative approach that is transforming capacitor charging processes. Utilizing principles of electromagnetic induction, wireless energy transfer allows capacitors to charge without direct physical connections. This technology is particularly beneficial in applications where traditional charging methods are impractical, such as in medical devices and consumer electronics.
C. Energy Harvesting Techniques
Energy harvesting techniques focus on capturing ambient energy to charge capacitors, making them ideal for low-power devices. By harnessing energy from sources such as solar, thermal, or kinetic energy, these methods enable capacitors to charge sustainably, reducing reliance on traditional power sources. This approach is particularly valuable in remote or off-grid applications.
VI. Quality Control and Testing in Manufacturing
A. Importance of Quality Assurance in Capacitor Charging
Quality assurance is paramount in capacitor manufacturing, as even minor defects can lead to significant failures in electronic systems. Ensuring that capacitors meet stringent quality standards is essential for maintaining reliability and performance.
B. Latest Testing Methodologies
Recent advancements in testing methodologies have improved the quality control process:
1. **Automated Testing Systems**: These systems allow for rapid and accurate testing of capacitors, ensuring they meet specifications before leaving the production line.
2. **Non-Destructive Testing Techniques**: Methods such as X-ray imaging and ultrasonic testing enable manufacturers to assess the integrity of capacitors without damaging them, providing valuable insights into potential defects.
C. Compliance with Industry Standards and Regulations
Manufacturers must adhere to industry standards and regulations to ensure the safety and reliability of their products. Compliance with standards such as IEC, UL, and RoHS is essential for gaining market acceptance and ensuring consumer trust.
VII. Future Trends in Capacitor Charging Manufacturing
A. Predictions for the Next Decade
The next decade is expected to witness significant advancements in capacitor charging manufacturing. As technology continues to evolve, manufacturers will likely adopt more sophisticated automation and smart manufacturing techniques, further enhancing efficiency and quality.
B. Potential Impact of Emerging Technologies
Emerging technologies such as artificial intelligence (AI) and machine learning are poised to revolutionize capacitor manufacturing. These technologies can optimize production processes, predict maintenance needs, and enhance quality control, leading to more efficient and reliable capacitor charging.
C. Sustainability and Eco-Friendly Practices
Sustainability is becoming increasingly important in manufacturing. Capacitor manufacturers are exploring eco-friendly practices, such as using recyclable materials and reducing energy consumption during production. These efforts not only benefit the environment but also align with consumer demand for sustainable products.
VIII. Conclusion
In conclusion, the landscape of capacitor charging manufacturing is evolving rapidly, driven by advancements in technology and a growing emphasis on quality and sustainability. From automation and smart manufacturing to innovative charging techniques, the industry is poised for significant growth and improvement. As we look to the future, continued research and development will be essential in enhancing the efficiency and performance of capacitor charging processes, ensuring that capacitors remain a vital component in the ever-evolving world of electronics.
IX. References
A comprehensive list of academic papers, industry reports, and relevant literature on capacitor charging and manufacturing processes would be included here to support the information presented in the article.
---
This blog post provides a detailed overview of the latest manufacturing processes for capacitor charging, highlighting the importance of innovation and quality in the industry.