What are the Latest Manufacturing Processes for Capacitor Discharge?
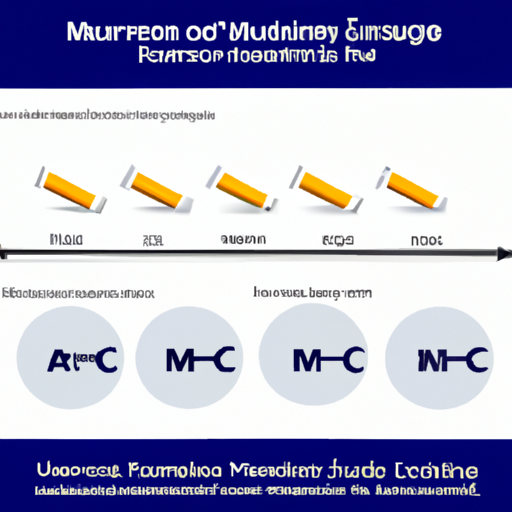
I. Introduction
Capacitor discharge is a fundamental process in electronics, where energy stored in a capacitor is released to power devices or systems. This process is crucial in various applications, from powering flash photography to providing energy in electric vehicles and renewable energy systems. As technology advances, the manufacturing processes for capacitors and their discharge mechanisms have evolved significantly. This blog post explores the latest manufacturing processes for capacitor discharge, highlighting innovations, challenges, and future directions in the industry.
II. Historical Context
A. Evolution of Capacitor Technology
Capacitors have been integral to electronic circuits since their inception in the 18th century. Initially, capacitors were simple devices made from glass or oil-filled jars. Over the decades, advancements in materials and design have led to the development of various capacitor types, including electrolytic, ceramic, and film capacitors. Each type has its unique characteristics, making them suitable for different applications.
B. Traditional Manufacturing Processes
Historically, the manufacturing of capacitors involved labor-intensive processes, including manual assembly and basic machining techniques. These methods, while effective, often resulted in inconsistencies in quality and performance. The reliance on traditional materials, such as aluminum and tantalum, also limited the energy density and efficiency of capacitors.
C. Limitations of Older Methods
Older manufacturing methods faced several limitations, including high production costs, longer lead times, and environmental concerns related to material waste and energy consumption. As the demand for more efficient and compact capacitors grew, the industry recognized the need for innovative manufacturing processes to overcome these challenges.
III. Current Trends in Capacitor Discharge Manufacturing
A. Advancements in Materials
1. Dielectric Materials
Recent advancements in dielectric materials have significantly improved capacitor performance. New materials, such as high-k dielectrics, allow for greater energy storage in smaller volumes. These materials enhance the capacitance and reduce leakage currents, making capacitors more efficient.
2. Conductive Materials
Innovations in conductive materials, including graphene and carbon nanotubes, have also transformed capacitor manufacturing. These materials offer superior conductivity and mechanical strength, enabling the production of capacitors that can withstand higher voltages and temperatures.
B. Innovations in Design
1. Miniaturization
The trend towards miniaturization in electronics has driven the development of smaller, more efficient capacitors. Manufacturers are now able to produce capacitors that occupy less space while maintaining or even enhancing their performance. This is particularly important in the design of compact electronic devices, such as smartphones and wearables.
2. Enhanced Energy Density
With the increasing demand for energy-efficient devices, manufacturers are focusing on enhancing the energy density of capacitors. This involves optimizing the design and materials used in capacitors to store more energy in a smaller footprint, which is essential for applications like electric vehicles and renewable energy systems.
C. Integration of Smart Technologies
1. IoT and Smart Capacitors
The integration of Internet of Things (IoT) technology into capacitor design has led to the development of smart capacitors. These capacitors can communicate with other devices, providing real-time data on their performance and health. This capability allows for better monitoring and management of energy storage systems.
2. Self-monitoring Capacitors
Self-monitoring capacitors are equipped with sensors that track their performance metrics, such as temperature and voltage. This data can be used to predict failures and optimize performance, reducing downtime and maintenance costs.
IV. Latest Manufacturing Techniques
A. Additive Manufacturing (3D Printing)
1. Benefits and Applications
Additive manufacturing, or 3D printing, has emerged as a revolutionary technique in capacitor manufacturing. This method allows for the precise layering of materials, enabling the creation of complex capacitor geometries that were previously impossible to achieve. The benefits include reduced material waste, faster prototyping, and the ability to customize designs for specific applications.
2. Case Studies
Several companies have successfully implemented 3D printing in capacitor manufacturing. For instance, researchers at a leading university have developed a 3D-printed supercapacitor that demonstrates significantly higher energy density compared to traditional capacitors. This innovation could pave the way for more efficient energy storage solutions in the future.
B. Automated Assembly Processes
1. Robotics in Manufacturing
The use of robotics in capacitor manufacturing has streamlined production processes, improving efficiency and consistency. Automated assembly lines can produce capacitors at a much faster rate than manual methods, reducing labor costs and minimizing human error.
2. Quality Control Measures
Advanced quality control measures, including machine learning algorithms and real-time monitoring systems, are now being employed to ensure the reliability and performance of capacitors. These technologies can detect defects early in the manufacturing process, leading to higher quality products and reduced waste.
C. Advanced Coating Techniques
1. Thin Film Technologies
Thin film technologies have revolutionized the way capacitors are coated, enhancing their performance and durability. These coatings can improve the dielectric properties of capacitors, leading to better energy storage capabilities and longer lifespans.
2. Surface Treatments
Surface treatments, such as plasma treatment and chemical vapor deposition, are being used to enhance the surface properties of capacitors. These treatments can improve adhesion, reduce surface roughness, and enhance the overall performance of the capacitor.
V. Environmental Considerations
A. Sustainable Manufacturing Practices
1. Recycling of Materials
As environmental concerns grow, the capacitor manufacturing industry is increasingly focusing on sustainable practices. Recycling materials used in capacitor production not only reduces waste but also lowers the demand for raw materials, contributing to a more sustainable manufacturing process.
2. Energy-efficient Processes
Manufacturers are also adopting energy-efficient processes to minimize their carbon footprint. This includes optimizing production techniques and investing in renewable energy sources to power manufacturing facilities.
B. Regulatory Compliance
1. Environmental Standards
Compliance with environmental standards is becoming a critical aspect of capacitor manufacturing. Manufacturers must adhere to regulations that govern the use of hazardous materials and waste management, ensuring that their processes are environmentally friendly.
2. Impact on Manufacturing Choices
The need for regulatory compliance is influencing manufacturing choices, pushing companies to invest in cleaner technologies and sustainable materials. This shift not only benefits the environment but also enhances the reputation of manufacturers in the eyes of consumers.
VI. Challenges in Capacitor Discharge Manufacturing
A. Technical Challenges
1. Material Limitations
Despite advancements in materials, challenges remain in finding suitable alternatives that can meet the performance requirements of modern capacitors. The search for new materials that offer higher energy density and better thermal stability continues to be a priority for researchers and manufacturers.
2. Production Scalability
Scaling up new manufacturing processes can be challenging. While innovative techniques like 3D printing show promise, transitioning from small-scale production to mass manufacturing requires significant investment and development.
B. Market Competition
1. Global Supply Chain Issues
The capacitor manufacturing industry faces intense competition, both domestically and internationally. Global supply chain issues, exacerbated by recent geopolitical tensions and the COVID-19 pandemic, have created challenges in sourcing materials and maintaining production schedules.
2. Cost Management
Cost management remains a critical concern for manufacturers. As the demand for advanced capacitors grows, companies must balance the costs of innovation with the need to remain competitive in pricing.
VII. Future Directions
A. Emerging Technologies
1. Nanotechnology in Capacitor Manufacturing
Nanotechnology is poised to play a significant role in the future of capacitor manufacturing. By manipulating materials at the nanoscale, manufacturers can create capacitors with enhanced performance characteristics, such as increased energy density and faster charge/discharge rates.
2. Quantum Capacitors
Quantum capacitors, which leverage quantum mechanics to store energy, represent a groundbreaking area of research. While still in the experimental stage, these capacitors could revolutionize energy storage and discharge processes in the future.
B. Predictions for the Industry
1. Market Growth
The capacitor market is expected to grow significantly in the coming years, driven by the increasing demand for energy-efficient devices and renewable energy solutions. Manufacturers that embrace innovative processes and sustainable practices will likely lead the way in this growth.
2. Innovations on the Horizon
As technology continues to advance, we can expect to see further innovations in capacitor design and manufacturing processes. From smart capacitors to advanced materials, the future of capacitor discharge manufacturing is bright and full of potential.
VIII. Conclusion
In summary, the manufacturing processes for capacitor discharge have evolved dramatically over the years, driven by advancements in materials, design, and technology. While challenges remain, the industry is poised for growth and innovation. Staying updated with the latest manufacturing processes is essential for manufacturers and consumers alike, as it will shape the future of energy storage and discharge applications. As we look ahead, the potential for new technologies and sustainable practices will undoubtedly play a crucial role in the continued evolution of capacitor discharge manufacturing.
IX. References
- Academic Journals
- Industry Reports
- Relevant Books and Articles
This blog post provides a comprehensive overview of the latest manufacturing processes for capacitor discharge, highlighting the importance of innovation and sustainability in the industry. As technology continues to advance, the future of capacitor manufacturing looks promising, with exciting developments on the horizon.
What are the Latest Manufacturing Processes for Capacitor Discharge?
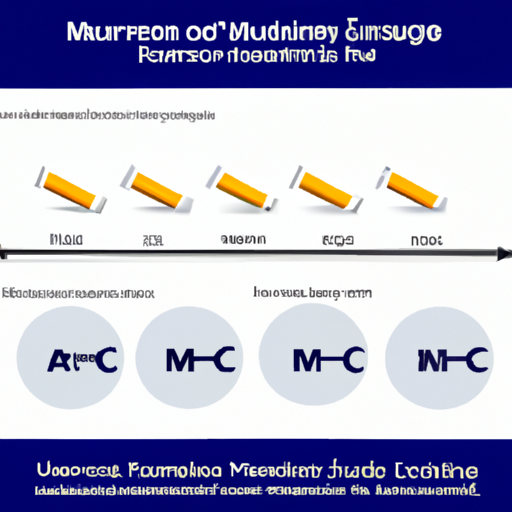
I. Introduction
Capacitor discharge is a fundamental process in electronics, where energy stored in a capacitor is released to power devices or systems. This process is crucial in various applications, from powering flash photography to providing energy in electric vehicles and renewable energy systems. As technology advances, the manufacturing processes for capacitors and their discharge mechanisms have evolved significantly. This blog post explores the latest manufacturing processes for capacitor discharge, highlighting innovations, challenges, and future directions in the industry.
II. Historical Context
A. Evolution of Capacitor Technology
Capacitors have been integral to electronic circuits since their inception in the 18th century. Initially, capacitors were simple devices made from glass or oil-filled jars. Over the decades, advancements in materials and design have led to the development of various capacitor types, including electrolytic, ceramic, and film capacitors. Each type has its unique characteristics, making them suitable for different applications.
B. Traditional Manufacturing Processes
Historically, the manufacturing of capacitors involved labor-intensive processes, including manual assembly and basic machining techniques. These methods, while effective, often resulted in inconsistencies in quality and performance. The reliance on traditional materials, such as aluminum and tantalum, also limited the energy density and efficiency of capacitors.
C. Limitations of Older Methods
Older manufacturing methods faced several limitations, including high production costs, longer lead times, and environmental concerns related to material waste and energy consumption. As the demand for more efficient and compact capacitors grew, the industry recognized the need for innovative manufacturing processes to overcome these challenges.
III. Current Trends in Capacitor Discharge Manufacturing
A. Advancements in Materials
1. Dielectric Materials
Recent advancements in dielectric materials have significantly improved capacitor performance. New materials, such as high-k dielectrics, allow for greater energy storage in smaller volumes. These materials enhance the capacitance and reduce leakage currents, making capacitors more efficient.
2. Conductive Materials
Innovations in conductive materials, including graphene and carbon nanotubes, have also transformed capacitor manufacturing. These materials offer superior conductivity and mechanical strength, enabling the production of capacitors that can withstand higher voltages and temperatures.
B. Innovations in Design
1. Miniaturization
The trend towards miniaturization in electronics has driven the development of smaller, more efficient capacitors. Manufacturers are now able to produce capacitors that occupy less space while maintaining or even enhancing their performance. This is particularly important in the design of compact electronic devices, such as smartphones and wearables.
2. Enhanced Energy Density
With the increasing demand for energy-efficient devices, manufacturers are focusing on enhancing the energy density of capacitors. This involves optimizing the design and materials used in capacitors to store more energy in a smaller footprint, which is essential for applications like electric vehicles and renewable energy systems.
C. Integration of Smart Technologies
1. IoT and Smart Capacitors
The integration of Internet of Things (IoT) technology into capacitor design has led to the development of smart capacitors. These capacitors can communicate with other devices, providing real-time data on their performance and health. This capability allows for better monitoring and management of energy storage systems.
2. Self-monitoring Capacitors
Self-monitoring capacitors are equipped with sensors that track their performance metrics, such as temperature and voltage. This data can be used to predict failures and optimize performance, reducing downtime and maintenance costs.
IV. Latest Manufacturing Techniques
A. Additive Manufacturing (3D Printing)
1. Benefits and Applications
Additive manufacturing, or 3D printing, has emerged as a revolutionary technique in capacitor manufacturing. This method allows for the precise layering of materials, enabling the creation of complex capacitor geometries that were previously impossible to achieve. The benefits include reduced material waste, faster prototyping, and the ability to customize designs for specific applications.
2. Case Studies
Several companies have successfully implemented 3D printing in capacitor manufacturing. For instance, researchers at a leading university have developed a 3D-printed supercapacitor that demonstrates significantly higher energy density compared to traditional capacitors. This innovation could pave the way for more efficient energy storage solutions in the future.
B. Automated Assembly Processes
1. Robotics in Manufacturing
The use of robotics in capacitor manufacturing has streamlined production processes, improving efficiency and consistency. Automated assembly lines can produce capacitors at a much faster rate than manual methods, reducing labor costs and minimizing human error.
2. Quality Control Measures
Advanced quality control measures, including machine learning algorithms and real-time monitoring systems, are now being employed to ensure the reliability and performance of capacitors. These technologies can detect defects early in the manufacturing process, leading to higher quality products and reduced waste.
C. Advanced Coating Techniques
1. Thin Film Technologies
Thin film technologies have revolutionized the way capacitors are coated, enhancing their performance and durability. These coatings can improve the dielectric properties of capacitors, leading to better energy storage capabilities and longer lifespans.
2. Surface Treatments
Surface treatments, such as plasma treatment and chemical vapor deposition, are being used to enhance the surface properties of capacitors. These treatments can improve adhesion, reduce surface roughness, and enhance the overall performance of the capacitor.
V. Environmental Considerations
A. Sustainable Manufacturing Practices
1. Recycling of Materials
As environmental concerns grow, the capacitor manufacturing industry is increasingly focusing on sustainable practices. Recycling materials used in capacitor production not only reduces waste but also lowers the demand for raw materials, contributing to a more sustainable manufacturing process.
2. Energy-efficient Processes
Manufacturers are also adopting energy-efficient processes to minimize their carbon footprint. This includes optimizing production techniques and investing in renewable energy sources to power manufacturing facilities.
B. Regulatory Compliance
1. Environmental Standards
Compliance with environmental standards is becoming a critical aspect of capacitor manufacturing. Manufacturers must adhere to regulations that govern the use of hazardous materials and waste management, ensuring that their processes are environmentally friendly.
2. Impact on Manufacturing Choices
The need for regulatory compliance is influencing manufacturing choices, pushing companies to invest in cleaner technologies and sustainable materials. This shift not only benefits the environment but also enhances the reputation of manufacturers in the eyes of consumers.
VI. Challenges in Capacitor Discharge Manufacturing
A. Technical Challenges
1. Material Limitations
Despite advancements in materials, challenges remain in finding suitable alternatives that can meet the performance requirements of modern capacitors. The search for new materials that offer higher energy density and better thermal stability continues to be a priority for researchers and manufacturers.
2. Production Scalability
Scaling up new manufacturing processes can be challenging. While innovative techniques like 3D printing show promise, transitioning from small-scale production to mass manufacturing requires significant investment and development.
B. Market Competition
1. Global Supply Chain Issues
The capacitor manufacturing industry faces intense competition, both domestically and internationally. Global supply chain issues, exacerbated by recent geopolitical tensions and the COVID-19 pandemic, have created challenges in sourcing materials and maintaining production schedules.
2. Cost Management
Cost management remains a critical concern for manufacturers. As the demand for advanced capacitors grows, companies must balance the costs of innovation with the need to remain competitive in pricing.
VII. Future Directions
A. Emerging Technologies
1. Nanotechnology in Capacitor Manufacturing
Nanotechnology is poised to play a significant role in the future of capacitor manufacturing. By manipulating materials at the nanoscale, manufacturers can create capacitors with enhanced performance characteristics, such as increased energy density and faster charge/discharge rates.
2. Quantum Capacitors
Quantum capacitors, which leverage quantum mechanics to store energy, represent a groundbreaking area of research. While still in the experimental stage, these capacitors could revolutionize energy storage and discharge processes in the future.
B. Predictions for the Industry
1. Market Growth
The capacitor market is expected to grow significantly in the coming years, driven by the increasing demand for energy-efficient devices and renewable energy solutions. Manufacturers that embrace innovative processes and sustainable practices will likely lead the way in this growth.
2. Innovations on the Horizon
As technology continues to advance, we can expect to see further innovations in capacitor design and manufacturing processes. From smart capacitors to advanced materials, the future of capacitor discharge manufacturing is bright and full of potential.
VIII. Conclusion
In summary, the manufacturing processes for capacitor discharge have evolved dramatically over the years, driven by advancements in materials, design, and technology. While challenges remain, the industry is poised for growth and innovation. Staying updated with the latest manufacturing processes is essential for manufacturers and consumers alike, as it will shape the future of energy storage and discharge applications. As we look ahead, the potential for new technologies and sustainable practices will undoubtedly play a crucial role in the continued evolution of capacitor discharge manufacturing.
IX. References
- Academic Journals
- Industry Reports
- Relevant Books and Articles
This blog post provides a comprehensive overview of the latest manufacturing processes for capacitor discharge, highlighting the importance of innovation and sustainability in the industry. As technology continues to advance, the future of capacitor manufacturing looks promising, with exciting developments on the horizon.