What are the Product Standards of Capacitor Manufacturers?
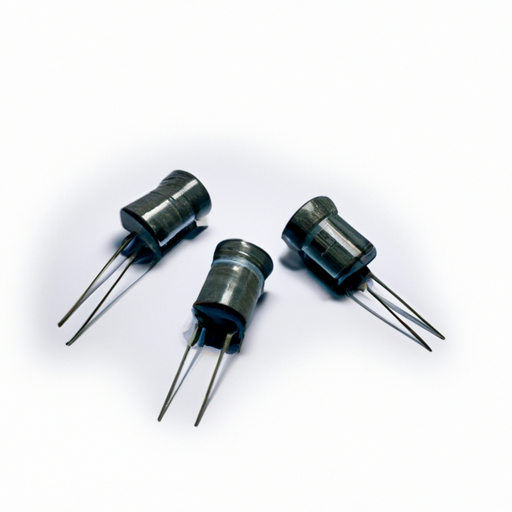
I. Introduction
Capacitors are essential components in electronic circuits, serving various functions such as energy storage, filtering, and signal coupling. As the demand for reliable and efficient electronic devices continues to grow, the importance of product standards in capacitor manufacturing cannot be overstated. These standards ensure that capacitors meet specific quality, safety, and performance criteria, ultimately protecting consumers and manufacturers alike. This article will explore the product standards of capacitor manufacturers, detailing the key standards, types of capacitors, testing methods, compliance processes, and future trends in the industry.
II. Understanding Capacitor Standards
A. Definition of Product Standards
Product standards are established criteria that define the quality, safety, and performance requirements for specific products. In the context of capacitors, these standards guide manufacturers in designing and producing components that are reliable and safe for use in various applications.
B. Role of Standards in Ensuring Quality and Safety
Standards play a crucial role in ensuring that capacitors function as intended and do not pose risks to users or equipment. By adhering to established standards, manufacturers can minimize defects, enhance product reliability, and ensure compliance with safety regulations.
C. Overview of International and National Standards Organizations
Numerous organizations develop and maintain standards for capacitors, including international bodies like the International Electrotechnical Commission (IEC) and the Institute of Electrical and Electronics Engineers (IEEE), as well as national organizations like the American National Standards Institute (ANSI) and Underwriters Laboratories (UL). These organizations work collaboratively to create comprehensive standards that address various aspects of capacitor design, manufacturing, and testing.
III. Key Standards for Capacitor Manufacturers
A. International Electrotechnical Commission (IEC)
The IEC is a leading organization in the development of international standards for electrical and electronic devices. Key standards for capacitors include:
1. **IEC 60384** - This standard specifies the requirements for fixed capacitors used in electronic equipment, covering aspects such as electrical characteristics, testing methods, and safety considerations.
2. **IEC 61071** - This standard focuses on capacitors for power electronics, addressing performance criteria and testing methods to ensure reliability in high-power applications.
B. Institute of Electrical and Electronics Engineers (IEEE)
The IEEE is a prominent organization that develops standards for electrical and electronic systems. Important standards for capacitors include:
1. **IEEE 18** - This standard outlines the measurement of capacitance, providing guidelines for accurate testing and evaluation of capacitor performance.
2. **IEEE 62** - This standard addresses the application of capacitors in power systems, ensuring that capacitors are used effectively and safely in electrical networks.
C. American National Standards Institute (ANSI)
ANSI oversees the development of standards in the United States. Relevant standards for capacitors include:
1. **ANSI C37** - This standard provides guidelines for power capacitors, including performance requirements and testing methods.
2. **ANSI/IEEE C57.12.01** - This standard covers transformers and capacitors, ensuring compatibility and safety in electrical systems.
D. Underwriters Laboratories (UL)
UL is a global safety certification organization that develops standards for product safety. Key standards for capacitors include:
1. **UL 810** - This standard specifies safety requirements for capacitors, addressing potential hazards and ensuring safe operation.
2. **UL 1414** - This standard focuses on the safety of capacitors used in various applications, providing guidelines for testing and evaluation.
E. Other Relevant Standards
In addition to the aforementioned standards, manufacturers must also consider regulations such as RoHS (Restriction of Hazardous Substances) and REACH (Registration, Evaluation, Authorisation, and Restriction of Chemicals), which address environmental and safety concerns related to the materials used in capacitor production.
IV. Types of Capacitors and Their Specific Standards
Capacitors come in various types, each with specific standards that address their unique characteristics and applications.
A. Electrolytic Capacitors
Electrolytic capacitors are widely used in power supply applications. Standards related to these capacitors focus on voltage ratings, capacitance values, and temperature stability to ensure reliable performance.
B. Ceramic Capacitors
Ceramic capacitors are known for their stability and reliability. Standards for these capacitors emphasize the quality of dielectric materials and performance characteristics, ensuring they meet the demands of high-frequency applications.
C. Film Capacitors
Film capacitors are used in various applications, including audio and power electronics. Standards for film capacitors address construction quality, dielectric properties, and long-term reliability to ensure consistent performance.
D. Tantalum Capacitors
Tantalum capacitors are known for their high capacitance values in a small package. Standards for these capacitors focus on safety and performance, particularly regarding failure modes and reliability under stress.
V. Testing and Quality Assurance
A. Importance of Testing in Capacitor Manufacturing
Testing is a critical aspect of capacitor manufacturing, ensuring that products meet established standards and perform reliably in their intended applications. Rigorous testing helps identify defects and ensures that capacitors can withstand the conditions they will encounter in real-world use.
B. Common Testing Methods
1. **Capacitance Measurement** - This method evaluates the capacitance value of a capacitor, ensuring it meets specified tolerances.
2. **Insulation Resistance Testing** - This test measures the insulation resistance of capacitors, ensuring they do not leak current and maintain safety.
3. **Dielectric Strength Testing** - This test assesses the ability of a capacitor to withstand high voltage without breaking down, ensuring safety and reliability.
C. Quality Assurance Processes
Quality assurance processes in capacitor manufacturing include:
1. **Incoming Material Inspection** - Raw materials are inspected to ensure they meet quality standards before production begins.
2. **In-Process Quality Checks** - Regular checks during the manufacturing process help identify and address issues early.
3. **Final Product Testing** - Comprehensive testing of finished capacitors ensures they meet all performance and safety standards before being shipped to customers.
VI. Compliance and Certification
A. Importance of Compliance with Standards
Compliance with established standards is essential for manufacturers to ensure product safety, reliability, and market acceptance. Non-compliance can lead to product recalls, legal issues, and damage to a manufacturer's reputation.
B. Certification Processes for Manufacturers
1. **ISO 9001** - This standard focuses on quality management systems, ensuring that manufacturers have processes in place to consistently produce high-quality products.
2. **ISO 14001** - This standard addresses environmental management systems, helping manufacturers minimize their environmental impact and comply with regulations.
C. Role of Third-Party Testing and Certification Bodies
Third-party testing and certification bodies play a vital role in verifying compliance with standards. These organizations conduct independent evaluations of products and manufacturing processes, providing manufacturers with credibility and assurance of quality.
VII. Challenges in Meeting Product Standards
A. Technological Advancements and Evolving Standards
As technology advances, product standards must evolve to address new materials, designs, and applications. Manufacturers must stay informed about changes in standards and adapt their processes accordingly.
B. Cost Implications of Compliance
Meeting product standards can involve significant costs, including investments in testing equipment, quality assurance processes, and training. Manufacturers must balance these costs with the need to produce high-quality products.
C. Globalization and Varying Standards Across Regions
Globalization has led to varying standards across different regions, complicating compliance for manufacturers operating in multiple markets. Understanding and navigating these differences is essential for successful international operations.
VIII. Future Trends in Capacitor Standards
A. Increasing Focus on Sustainability and Environmental Impact
As environmental concerns grow, there is an increasing focus on sustainability in capacitor manufacturing. Standards are likely to evolve to address the environmental impact of materials and production processes.
B. Innovations in Capacitor Technology and Their Implications for Standards
Innovations in capacitor technology, such as the development of new materials and designs, will necessitate updates to existing standards to ensure they remain relevant and effective.
C. Anticipated Changes in Regulatory Frameworks
Regulatory frameworks governing capacitor manufacturing are expected to evolve, with an emphasis on safety, environmental impact, and consumer protection. Manufacturers must stay informed about these changes to ensure compliance.
IX. Conclusion
In conclusion, product standards play a vital role in the manufacturing of capacitors, ensuring safety, reliability, and performance. By adhering to established standards, manufacturers can produce high-quality products that meet the demands of various applications. As technology advances and environmental concerns grow, the landscape of capacitor standards will continue to evolve, presenting both challenges and opportunities for manufacturers. Staying informed and compliant with these standards will be essential for success in the ever-changing electronics industry.
X. References
- International Electrotechnical Commission (IEC)
- Institute of Electrical and Electronics Engineers (IEEE)
- American National Standards Institute (ANSI)
- Underwriters Laboratories (UL)
- ISO 9001 and ISO 14001 Standards
- RoHS and REACH Regulations
This comprehensive overview of the product standards of capacitor manufacturers highlights the importance of quality and safety in the industry, providing valuable insights for manufacturers, engineers, and consumers alike.
What are the Product Standards of Capacitor Manufacturers?
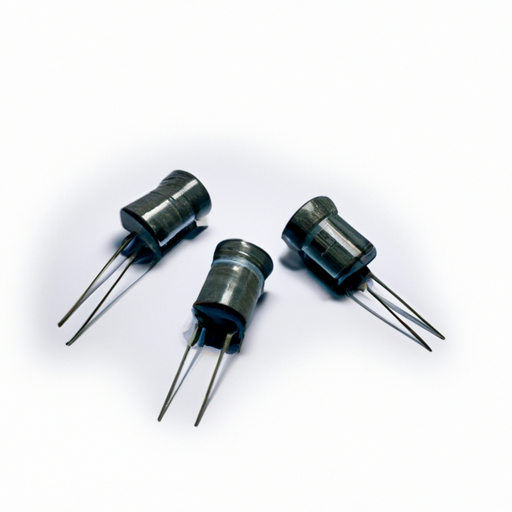
I. Introduction
Capacitors are essential components in electronic circuits, serving various functions such as energy storage, filtering, and signal coupling. As the demand for reliable and efficient electronic devices continues to grow, the importance of product standards in capacitor manufacturing cannot be overstated. These standards ensure that capacitors meet specific quality, safety, and performance criteria, ultimately protecting consumers and manufacturers alike. This article will explore the product standards of capacitor manufacturers, detailing the key standards, types of capacitors, testing methods, compliance processes, and future trends in the industry.
II. Understanding Capacitor Standards
A. Definition of Product Standards
Product standards are established criteria that define the quality, safety, and performance requirements for specific products. In the context of capacitors, these standards guide manufacturers in designing and producing components that are reliable and safe for use in various applications.
B. Role of Standards in Ensuring Quality and Safety
Standards play a crucial role in ensuring that capacitors function as intended and do not pose risks to users or equipment. By adhering to established standards, manufacturers can minimize defects, enhance product reliability, and ensure compliance with safety regulations.
C. Overview of International and National Standards Organizations
Numerous organizations develop and maintain standards for capacitors, including international bodies like the International Electrotechnical Commission (IEC) and the Institute of Electrical and Electronics Engineers (IEEE), as well as national organizations like the American National Standards Institute (ANSI) and Underwriters Laboratories (UL). These organizations work collaboratively to create comprehensive standards that address various aspects of capacitor design, manufacturing, and testing.
III. Key Standards for Capacitor Manufacturers
A. International Electrotechnical Commission (IEC)
The IEC is a leading organization in the development of international standards for electrical and electronic devices. Key standards for capacitors include:
1. **IEC 60384** - This standard specifies the requirements for fixed capacitors used in electronic equipment, covering aspects such as electrical characteristics, testing methods, and safety considerations.
2. **IEC 61071** - This standard focuses on capacitors for power electronics, addressing performance criteria and testing methods to ensure reliability in high-power applications.
B. Institute of Electrical and Electronics Engineers (IEEE)
The IEEE is a prominent organization that develops standards for electrical and electronic systems. Important standards for capacitors include:
1. **IEEE 18** - This standard outlines the measurement of capacitance, providing guidelines for accurate testing and evaluation of capacitor performance.
2. **IEEE 62** - This standard addresses the application of capacitors in power systems, ensuring that capacitors are used effectively and safely in electrical networks.
C. American National Standards Institute (ANSI)
ANSI oversees the development of standards in the United States. Relevant standards for capacitors include:
1. **ANSI C37** - This standard provides guidelines for power capacitors, including performance requirements and testing methods.
2. **ANSI/IEEE C57.12.01** - This standard covers transformers and capacitors, ensuring compatibility and safety in electrical systems.
D. Underwriters Laboratories (UL)
UL is a global safety certification organization that develops standards for product safety. Key standards for capacitors include:
1. **UL 810** - This standard specifies safety requirements for capacitors, addressing potential hazards and ensuring safe operation.
2. **UL 1414** - This standard focuses on the safety of capacitors used in various applications, providing guidelines for testing and evaluation.
E. Other Relevant Standards
In addition to the aforementioned standards, manufacturers must also consider regulations such as RoHS (Restriction of Hazardous Substances) and REACH (Registration, Evaluation, Authorisation, and Restriction of Chemicals), which address environmental and safety concerns related to the materials used in capacitor production.
IV. Types of Capacitors and Their Specific Standards
Capacitors come in various types, each with specific standards that address their unique characteristics and applications.
A. Electrolytic Capacitors
Electrolytic capacitors are widely used in power supply applications. Standards related to these capacitors focus on voltage ratings, capacitance values, and temperature stability to ensure reliable performance.
B. Ceramic Capacitors
Ceramic capacitors are known for their stability and reliability. Standards for these capacitors emphasize the quality of dielectric materials and performance characteristics, ensuring they meet the demands of high-frequency applications.
C. Film Capacitors
Film capacitors are used in various applications, including audio and power electronics. Standards for film capacitors address construction quality, dielectric properties, and long-term reliability to ensure consistent performance.
D. Tantalum Capacitors
Tantalum capacitors are known for their high capacitance values in a small package. Standards for these capacitors focus on safety and performance, particularly regarding failure modes and reliability under stress.
V. Testing and Quality Assurance
A. Importance of Testing in Capacitor Manufacturing
Testing is a critical aspect of capacitor manufacturing, ensuring that products meet established standards and perform reliably in their intended applications. Rigorous testing helps identify defects and ensures that capacitors can withstand the conditions they will encounter in real-world use.
B. Common Testing Methods
1. **Capacitance Measurement** - This method evaluates the capacitance value of a capacitor, ensuring it meets specified tolerances.
2. **Insulation Resistance Testing** - This test measures the insulation resistance of capacitors, ensuring they do not leak current and maintain safety.
3. **Dielectric Strength Testing** - This test assesses the ability of a capacitor to withstand high voltage without breaking down, ensuring safety and reliability.
C. Quality Assurance Processes
Quality assurance processes in capacitor manufacturing include:
1. **Incoming Material Inspection** - Raw materials are inspected to ensure they meet quality standards before production begins.
2. **In-Process Quality Checks** - Regular checks during the manufacturing process help identify and address issues early.
3. **Final Product Testing** - Comprehensive testing of finished capacitors ensures they meet all performance and safety standards before being shipped to customers.
VI. Compliance and Certification
A. Importance of Compliance with Standards
Compliance with established standards is essential for manufacturers to ensure product safety, reliability, and market acceptance. Non-compliance can lead to product recalls, legal issues, and damage to a manufacturer's reputation.
B. Certification Processes for Manufacturers
1. **ISO 9001** - This standard focuses on quality management systems, ensuring that manufacturers have processes in place to consistently produce high-quality products.
2. **ISO 14001** - This standard addresses environmental management systems, helping manufacturers minimize their environmental impact and comply with regulations.
C. Role of Third-Party Testing and Certification Bodies
Third-party testing and certification bodies play a vital role in verifying compliance with standards. These organizations conduct independent evaluations of products and manufacturing processes, providing manufacturers with credibility and assurance of quality.
VII. Challenges in Meeting Product Standards
A. Technological Advancements and Evolving Standards
As technology advances, product standards must evolve to address new materials, designs, and applications. Manufacturers must stay informed about changes in standards and adapt their processes accordingly.
B. Cost Implications of Compliance
Meeting product standards can involve significant costs, including investments in testing equipment, quality assurance processes, and training. Manufacturers must balance these costs with the need to produce high-quality products.
C. Globalization and Varying Standards Across Regions
Globalization has led to varying standards across different regions, complicating compliance for manufacturers operating in multiple markets. Understanding and navigating these differences is essential for successful international operations.
VIII. Future Trends in Capacitor Standards
A. Increasing Focus on Sustainability and Environmental Impact
As environmental concerns grow, there is an increasing focus on sustainability in capacitor manufacturing. Standards are likely to evolve to address the environmental impact of materials and production processes.
B. Innovations in Capacitor Technology and Their Implications for Standards
Innovations in capacitor technology, such as the development of new materials and designs, will necessitate updates to existing standards to ensure they remain relevant and effective.
C. Anticipated Changes in Regulatory Frameworks
Regulatory frameworks governing capacitor manufacturing are expected to evolve, with an emphasis on safety, environmental impact, and consumer protection. Manufacturers must stay informed about these changes to ensure compliance.
IX. Conclusion
In conclusion, product standards play a vital role in the manufacturing of capacitors, ensuring safety, reliability, and performance. By adhering to established standards, manufacturers can produce high-quality products that meet the demands of various applications. As technology advances and environmental concerns grow, the landscape of capacitor standards will continue to evolve, presenting both challenges and opportunities for manufacturers. Staying informed and compliant with these standards will be essential for success in the ever-changing electronics industry.
X. References
- International Electrotechnical Commission (IEC)
- Institute of Electrical and Electronics Engineers (IEEE)
- American National Standards Institute (ANSI)
- Underwriters Laboratories (UL)
- ISO 9001 and ISO 14001 Standards
- RoHS and REACH Regulations
This comprehensive overview of the product standards of capacitor manufacturers highlights the importance of quality and safety in the industry, providing valuable insights for manufacturers, engineers, and consumers alike.