Common Production Processes for Power Wirewound Resistors
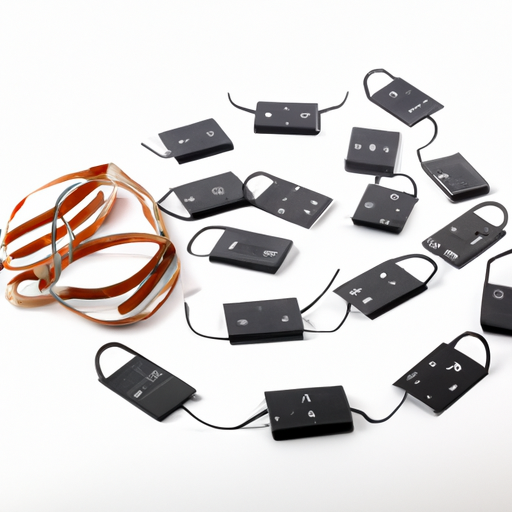
I. Introduction
Power wirewound resistors are essential components in various electronic applications, serving as critical elements for controlling current and voltage in circuits. These resistors are constructed by winding a conductive wire around a core, which allows for precise resistance values and high power ratings. Their importance cannot be overstated, as they are widely used in power supplies, amplifiers, and other electronic devices where reliability and performance are paramount. This blog post will explore the common production processes involved in manufacturing power wirewound resistors, highlighting the materials, design considerations, and production techniques that contribute to their effectiveness.
II. Materials Used in Power Wirewound Resistors
A. Conductive Wire Materials
The choice of conductive wire material is crucial in determining the performance of power wirewound resistors. Common materials include nickel-chromium and copper-nickel alloys, each offering unique properties that influence resistance, thermal stability, and overall performance.
1. **Nickel-Chromium**: This alloy is favored for its high-temperature stability and resistance to oxidation, making it suitable for high-power applications. Its ability to maintain consistent resistance values under varying temperatures is a significant advantage.
2. **Copper-Nickel**: Known for its excellent conductivity, copper-nickel is often used in applications where lower resistance values are required. However, it may not perform as well as nickel-chromium at elevated temperatures.
B. Insulating Materials
Insulation plays a vital role in the performance of wirewound resistors, preventing short circuits and ensuring safety during operation.
1. **Ceramic Insulation**: This is commonly used due to its high thermal resistance and ability to withstand high temperatures. Ceramic materials also provide excellent dielectric properties, making them ideal for high-power applications.
2. **Epoxy Insulation**: Epoxy resins are often used for their ease of application and ability to form a strong bond with the wire and core. They provide good electrical insulation and can be cured quickly, making them suitable for mass production.
C. Additional Components
In addition to the wire and insulation, several other components are essential for the assembly of power wirewound resistors.
1. **End Caps and Terminals**: These components are necessary for connecting the resistor to a circuit. They must be made from conductive materials that can withstand the thermal and mechanical stresses of operation.
2. **Heat Sinks and Mounting Hardware**: To dissipate heat generated during operation, heat sinks are often attached to wirewound resistors. Proper mounting hardware is also crucial for ensuring stability and reliability in various applications.
III. Design and Engineering Considerations
Before production begins, several design and engineering considerations must be addressed to ensure the resistor meets specific performance requirements.
A. Resistance Value Determination
The desired resistance value is a primary factor in the design process. Engineers must calculate the appropriate wire length and gauge to achieve the target resistance while considering the material's resistivity.
B. Power Rating Specifications
Power rating is another critical specification, as it determines how much power the resistor can handle without overheating. This rating is influenced by the wire material, insulation type, and overall design.
C. Tolerance and Temperature Coefficient Requirements
Tolerance refers to the allowable deviation from the specified resistance value, while the temperature coefficient indicates how much the resistance changes with temperature. Both factors are essential for ensuring the resistor performs reliably in varying conditions.
D. Customization Options for Specific Applications
Many applications require customized resistors tailored to specific needs. This may involve adjusting resistance values, power ratings, or physical dimensions to fit particular circuit designs.
IV. Production Processes
The production of power wirewound resistors involves several key processes, each requiring precision and attention to detail.
A. Wire Winding
The first step in the production process is wire winding, where the conductive wire is wound around a core material.
1. **Description of the Winding Process**: The wire is carefully wound in a specific pattern to achieve the desired resistance value. The number of turns and the tightness of the winding are critical factors that influence the final resistance.
2. **Equipment Used**: Specialized winding machines are employed to ensure uniformity and precision during the winding process. These machines can be programmed to create specific winding patterns and tensions.
3. **Importance of Precision in Winding**: Any inconsistencies in the winding can lead to variations in resistance and performance. Therefore, maintaining precision is crucial for producing high-quality resistors.
B. Core Preparation
Once the wire is wound, the core must be prepared to support the resistor's structure.
1. **Selection of Core Materials**: The choice of core material affects the resistor's thermal and electrical properties. Common materials include ceramic and metal, each offering different benefits.
2. **Core Shaping and Treatment**: The core may undergo shaping and treatment processes to enhance its performance. This can include processes like sintering for ceramic cores, which improves their strength and thermal stability.
C. Insulation Application
After the core is prepared, insulation is applied to protect the wire and enhance performance.
1. **Methods of Applying Insulation**: Insulation can be applied using various methods, including dipping, spraying, or wrapping. The chosen method depends on the type of insulation material and the desired thickness.
2. **Curing and Drying Processes**: Once the insulation is applied, it must be cured or dried to ensure proper adhesion and performance. This step is critical for epoxy-based insulations, which require specific temperature and time conditions to cure effectively.
D. Assembly
The assembly process involves joining the wire to terminals and securing the entire assembly in a housing.
1. **Joining the Wire to Terminals**: This step typically involves soldering or crimping the wire to the terminals, ensuring a reliable electrical connection.
2. **Securing the Assembly in a Housing**: The assembled resistor is then placed in a protective housing, which may also include heat sinks for thermal management.
E. Testing and Quality Control
Quality control is a vital part of the production process, ensuring that each resistor meets the required specifications.
1. **Electrical Testing**: This includes measuring resistance values and verifying power ratings to ensure compliance with design specifications.
2. **Mechanical Testing**: Resistors undergo mechanical testing, such as thermal cycling and vibration tests, to assess their durability and reliability under real-world conditions.
3. **Final Inspection and Certification**: Each resistor is subjected to a final inspection to ensure it meets all quality standards before being certified for use.
V. Post-Production Processes
Once the resistors are produced, several post-production processes are necessary to prepare them for market.
A. Packaging and Labeling
Proper packaging is essential to protect the resistors during shipping and storage. Each package is labeled with important information, including resistance values, power ratings, and safety warnings.
B. Shipping and Distribution
After packaging, the resistors are shipped to distributors or directly to customers. Efficient logistics are crucial to ensure timely delivery and customer satisfaction.
C. Customer Support and Warranty Considerations
Manufacturers often provide customer support and warranty options to address any issues that may arise after purchase. This support is vital for maintaining customer trust and satisfaction.
VI. Challenges in Production
The production of power wirewound resistors is not without its challenges.
A. Material Sourcing and Cost Fluctuations
Sourcing high-quality materials can be challenging, especially with fluctuations in prices and availability. Manufacturers must navigate these challenges to maintain production efficiency and cost-effectiveness.
B. Technological Advancements and Automation
As technology advances, manufacturers must adapt to new production techniques and automation processes. While automation can improve efficiency, it also requires investment in new equipment and training.
C. Environmental Considerations and Regulations
Manufacturers must also consider environmental regulations and sustainability practices. This includes managing waste, reducing energy consumption, and ensuring compliance with industry standards.
VII. Conclusion
In conclusion, the production processes for power wirewound resistors are complex and multifaceted, involving careful consideration of materials, design, and manufacturing techniques. As technology continues to evolve, the industry will likely see advancements that enhance efficiency and performance. Power wirewound resistors will remain a vital component in modern electronics, playing a crucial role in ensuring the reliability and functionality of various devices. Understanding these production processes not only highlights the intricacies of resistor manufacturing but also underscores the importance of quality and precision in the electronics industry.
Common Production Processes for Power Wirewound Resistors
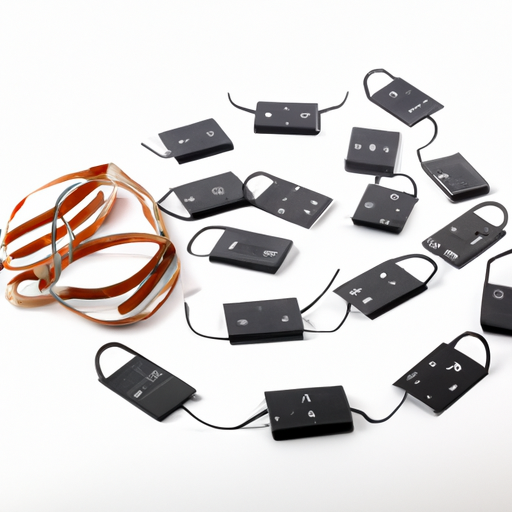
I. Introduction
Power wirewound resistors are essential components in various electronic applications, serving as critical elements for controlling current and voltage in circuits. These resistors are constructed by winding a conductive wire around a core, which allows for precise resistance values and high power ratings. Their importance cannot be overstated, as they are widely used in power supplies, amplifiers, and other electronic devices where reliability and performance are paramount. This blog post will explore the common production processes involved in manufacturing power wirewound resistors, highlighting the materials, design considerations, and production techniques that contribute to their effectiveness.
II. Materials Used in Power Wirewound Resistors
A. Conductive Wire Materials
The choice of conductive wire material is crucial in determining the performance of power wirewound resistors. Common materials include nickel-chromium and copper-nickel alloys, each offering unique properties that influence resistance, thermal stability, and overall performance.
1. **Nickel-Chromium**: This alloy is favored for its high-temperature stability and resistance to oxidation, making it suitable for high-power applications. Its ability to maintain consistent resistance values under varying temperatures is a significant advantage.
2. **Copper-Nickel**: Known for its excellent conductivity, copper-nickel is often used in applications where lower resistance values are required. However, it may not perform as well as nickel-chromium at elevated temperatures.
B. Insulating Materials
Insulation plays a vital role in the performance of wirewound resistors, preventing short circuits and ensuring safety during operation.
1. **Ceramic Insulation**: This is commonly used due to its high thermal resistance and ability to withstand high temperatures. Ceramic materials also provide excellent dielectric properties, making them ideal for high-power applications.
2. **Epoxy Insulation**: Epoxy resins are often used for their ease of application and ability to form a strong bond with the wire and core. They provide good electrical insulation and can be cured quickly, making them suitable for mass production.
C. Additional Components
In addition to the wire and insulation, several other components are essential for the assembly of power wirewound resistors.
1. **End Caps and Terminals**: These components are necessary for connecting the resistor to a circuit. They must be made from conductive materials that can withstand the thermal and mechanical stresses of operation.
2. **Heat Sinks and Mounting Hardware**: To dissipate heat generated during operation, heat sinks are often attached to wirewound resistors. Proper mounting hardware is also crucial for ensuring stability and reliability in various applications.
III. Design and Engineering Considerations
Before production begins, several design and engineering considerations must be addressed to ensure the resistor meets specific performance requirements.
A. Resistance Value Determination
The desired resistance value is a primary factor in the design process. Engineers must calculate the appropriate wire length and gauge to achieve the target resistance while considering the material's resistivity.
B. Power Rating Specifications
Power rating is another critical specification, as it determines how much power the resistor can handle without overheating. This rating is influenced by the wire material, insulation type, and overall design.
C. Tolerance and Temperature Coefficient Requirements
Tolerance refers to the allowable deviation from the specified resistance value, while the temperature coefficient indicates how much the resistance changes with temperature. Both factors are essential for ensuring the resistor performs reliably in varying conditions.
D. Customization Options for Specific Applications
Many applications require customized resistors tailored to specific needs. This may involve adjusting resistance values, power ratings, or physical dimensions to fit particular circuit designs.
IV. Production Processes
The production of power wirewound resistors involves several key processes, each requiring precision and attention to detail.
A. Wire Winding
The first step in the production process is wire winding, where the conductive wire is wound around a core material.
1. **Description of the Winding Process**: The wire is carefully wound in a specific pattern to achieve the desired resistance value. The number of turns and the tightness of the winding are critical factors that influence the final resistance.
2. **Equipment Used**: Specialized winding machines are employed to ensure uniformity and precision during the winding process. These machines can be programmed to create specific winding patterns and tensions.
3. **Importance of Precision in Winding**: Any inconsistencies in the winding can lead to variations in resistance and performance. Therefore, maintaining precision is crucial for producing high-quality resistors.
B. Core Preparation
Once the wire is wound, the core must be prepared to support the resistor's structure.
1. **Selection of Core Materials**: The choice of core material affects the resistor's thermal and electrical properties. Common materials include ceramic and metal, each offering different benefits.
2. **Core Shaping and Treatment**: The core may undergo shaping and treatment processes to enhance its performance. This can include processes like sintering for ceramic cores, which improves their strength and thermal stability.
C. Insulation Application
After the core is prepared, insulation is applied to protect the wire and enhance performance.
1. **Methods of Applying Insulation**: Insulation can be applied using various methods, including dipping, spraying, or wrapping. The chosen method depends on the type of insulation material and the desired thickness.
2. **Curing and Drying Processes**: Once the insulation is applied, it must be cured or dried to ensure proper adhesion and performance. This step is critical for epoxy-based insulations, which require specific temperature and time conditions to cure effectively.
D. Assembly
The assembly process involves joining the wire to terminals and securing the entire assembly in a housing.
1. **Joining the Wire to Terminals**: This step typically involves soldering or crimping the wire to the terminals, ensuring a reliable electrical connection.
2. **Securing the Assembly in a Housing**: The assembled resistor is then placed in a protective housing, which may also include heat sinks for thermal management.
E. Testing and Quality Control
Quality control is a vital part of the production process, ensuring that each resistor meets the required specifications.
1. **Electrical Testing**: This includes measuring resistance values and verifying power ratings to ensure compliance with design specifications.
2. **Mechanical Testing**: Resistors undergo mechanical testing, such as thermal cycling and vibration tests, to assess their durability and reliability under real-world conditions.
3. **Final Inspection and Certification**: Each resistor is subjected to a final inspection to ensure it meets all quality standards before being certified for use.
V. Post-Production Processes
Once the resistors are produced, several post-production processes are necessary to prepare them for market.
A. Packaging and Labeling
Proper packaging is essential to protect the resistors during shipping and storage. Each package is labeled with important information, including resistance values, power ratings, and safety warnings.
B. Shipping and Distribution
After packaging, the resistors are shipped to distributors or directly to customers. Efficient logistics are crucial to ensure timely delivery and customer satisfaction.
C. Customer Support and Warranty Considerations
Manufacturers often provide customer support and warranty options to address any issues that may arise after purchase. This support is vital for maintaining customer trust and satisfaction.
VI. Challenges in Production
The production of power wirewound resistors is not without its challenges.
A. Material Sourcing and Cost Fluctuations
Sourcing high-quality materials can be challenging, especially with fluctuations in prices and availability. Manufacturers must navigate these challenges to maintain production efficiency and cost-effectiveness.
B. Technological Advancements and Automation
As technology advances, manufacturers must adapt to new production techniques and automation processes. While automation can improve efficiency, it also requires investment in new equipment and training.
C. Environmental Considerations and Regulations
Manufacturers must also consider environmental regulations and sustainability practices. This includes managing waste, reducing energy consumption, and ensuring compliance with industry standards.
VII. Conclusion
In conclusion, the production processes for power wirewound resistors are complex and multifaceted, involving careful consideration of materials, design, and manufacturing techniques. As technology continues to evolve, the industry will likely see advancements that enhance efficiency and performance. Power wirewound resistors will remain a vital component in modern electronics, playing a crucial role in ensuring the reliability and functionality of various devices. Understanding these production processes not only highlights the intricacies of resistor manufacturing but also underscores the importance of quality and precision in the electronics industry.