Manufacturing Processes of the Latest Glass Glaze Resistors
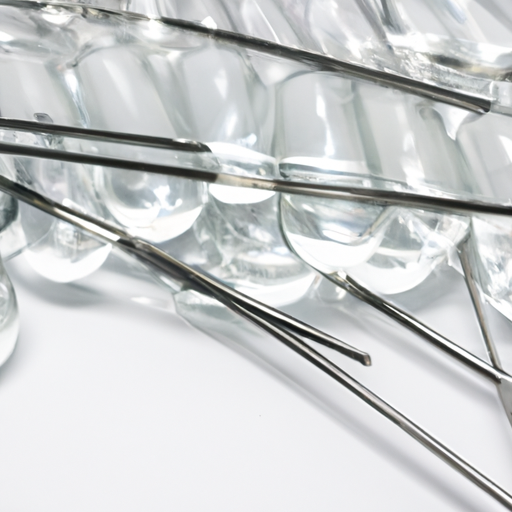
I. Introduction
In the world of electronics, resistors play a crucial role in controlling the flow of electric current. Among the various types of resistors, glass glaze resistors have gained prominence due to their unique properties and manufacturing processes. These resistors are characterized by a glass coating that provides excellent thermal stability, high resistance to environmental factors, and superior electrical performance. This blog post will delve into the manufacturing processes of the latest glass glaze resistors, exploring their historical context, materials, production techniques, quality control measures, innovations, and applications.
II. Historical Context
The evolution of resistor technology has been marked by significant advancements, from simple wire-wound resistors to more complex and efficient designs. Glass glaze resistors emerged as a response to the need for components that could withstand harsh environmental conditions while maintaining reliable performance. Unlike traditional carbon or metal film resistors, glass glaze resistors offer enhanced durability and stability, making them suitable for a wide range of applications. Their introduction marked a pivotal moment in resistor technology, providing engineers with a robust solution for demanding electronic circuits.
III. Materials Used in Glass Glaze Resistors
The performance of glass glaze resistors is heavily influenced by the materials used in their construction.
A. Composition of Glass Glaze
1. **Silica**: The primary component of glass glaze is silica, which forms the glass matrix. Silica provides the necessary thermal and electrical insulation properties.
2. **Fluxing Agents**: These materials lower the melting point of silica, facilitating the formation of a smooth and uniform glass layer. Common fluxing agents include boron oxide and sodium oxide.
3. **Colorants and Additives**: To achieve specific electrical characteristics and aesthetic qualities, various colorants and additives are incorporated into the glass glaze. These can enhance the visibility of the resistor's markings and improve its performance.
B. Conductive Materials
1. **Metal Oxides**: Metal oxides, such as tin oxide and indium oxide, are often used as the primary conductive materials in glass glaze resistors. They provide the necessary resistance values and stability.
2. **Carbon-Based Materials**: In some cases, carbon-based materials are added to improve conductivity and reduce the temperature coefficient of resistance.
C. Substrates
1. **Ceramic Bases**: The substrate for glass glaze resistors is typically made from ceramic materials, which offer excellent thermal stability and electrical insulation.
2. **Other Supporting Materials**: Depending on the application, other materials may be used to enhance the mechanical properties of the resistor.
IV. Manufacturing Processes
The manufacturing of glass glaze resistors involves several intricate processes, each contributing to the final product's quality and performance.
A. Preparation of Raw Materials
1. **Sourcing and Quality Control**: The first step in manufacturing glass glaze resistors is sourcing high-quality raw materials. Rigorous quality control measures are implemented to ensure that all materials meet industry standards.
2. **Mixing and Grinding**: The raw materials are then mixed and ground to achieve a uniform particle size. This step is crucial for ensuring consistent performance in the final product.
B. Forming the Resistor Body
1. **Molding Techniques**: The resistor body is formed using various molding techniques, such as pressing or casting. These methods allow for precise shaping of the resistor to meet specific design requirements.
2. **Extrusion Processes**: In some cases, extrusion processes are employed to create long, continuous shapes that can be cut to the desired length later.
C. Application of Glass Glaze
1. **Coating Techniques**: The application of glass glaze is a critical step in the manufacturing process. Several techniques can be used, including:
- **Dip Coating**: The resistor body is dipped into a molten glass glaze, allowing for a uniform coating.
- **Spray Coating**: A spray method can be used to apply a fine layer of glass glaze, ensuring even coverage.
- **Screen Printing**: This technique allows for precise application of the glass glaze in specific patterns or designs.
2. **Drying and Curing**: After the glaze is applied, the resistors undergo a drying and curing process to solidify the glass coating. This step is essential for achieving the desired mechanical and electrical properties.
D. Sintering Process
1. **Temperature Control**: The sintering process involves heating the coated resistors to a specific temperature, allowing the glass to fuse and bond with the substrate. Precise temperature control is critical to avoid damaging the resistor.
2. **Time Management**: The duration of the sintering process is also carefully managed to ensure optimal performance. Too short a time may result in incomplete bonding, while too long can lead to degradation of the materials.
E. Electrical Termination
1. **Attachment of Leads**: Once the resistors are sintered, electrical leads are attached to facilitate connection in electronic circuits. This step is crucial for ensuring reliable electrical performance.
2. **Soldering Techniques**: Various soldering techniques are employed to secure the leads, ensuring a strong and conductive connection.
V. Quality Control Measures
Quality control is paramount in the manufacturing of glass glaze resistors to ensure they meet the required specifications.
A. Testing for Electrical Properties
1. **Resistance Measurement**: Each resistor is tested for its resistance value to ensure it falls within the specified tolerance range.
2. **Tolerance Testing**: Tolerance testing is conducted to verify that the resistors can perform reliably under varying conditions.
B. Physical Inspection
1. **Visual Checks**: A thorough visual inspection is performed to identify any defects in the glass coating or resistor body.
2. **Dimensional Accuracy**: The dimensions of the resistors are measured to ensure they meet design specifications.
C. Environmental Testing
1. **Thermal Cycling**: Resistors undergo thermal cycling tests to evaluate their performance under extreme temperature variations.
2. **Humidity Resistance**: Humidity resistance tests are conducted to ensure that the resistors can withstand moisture without degradation.
VI. Innovations in Glass Glaze Resistor Manufacturing
The manufacturing processes for glass glaze resistors have seen significant innovations in recent years.
A. Advances in Material Science
New materials and formulations are being developed to enhance the performance and reliability of glass glaze resistors. These advancements contribute to improved thermal stability and reduced size.
B. Automation and Robotics in Production
The integration of automation and robotics in the manufacturing process has increased efficiency and precision. Automated systems can perform repetitive tasks with high accuracy, reducing the risk of human error.
C. Eco-Friendly Manufacturing Practices
As sustainability becomes a priority in manufacturing, eco-friendly practices are being adopted. This includes the use of recyclable materials and processes that minimize waste and energy consumption.
VII. Applications of Glass Glaze Resistors
Glass glaze resistors are utilized in a wide range of applications due to their unique properties.
A. Use in Consumer Electronics
These resistors are commonly found in consumer electronics, such as televisions, smartphones, and computers, where reliability and performance are critical.
B. Industrial Applications
In industrial settings, glass glaze resistors are used in machinery and equipment that require robust components capable of withstanding harsh conditions.
C. Automotive and Aerospace Industries
The automotive and aerospace industries rely on glass glaze resistors for their durability and performance in demanding environments, such as high temperatures and vibrations.
VIII. Conclusion
In summary, the manufacturing processes of glass glaze resistors involve a complex interplay of materials, techniques, and quality control measures. As technology continues to advance, the future of glass glaze resistor manufacturing looks promising, with innovations in material science, automation, and eco-friendly practices paving the way for enhanced performance and sustainability. The importance of continued innovation in this field cannot be overstated, as it ensures that electronic components remain reliable and efficient in an ever-evolving technological landscape.
IX. References
A comprehensive list of academic journals, industry reports, and manufacturer specifications would be included here to support the information presented in this blog post.
Manufacturing Processes of the Latest Glass Glaze Resistors
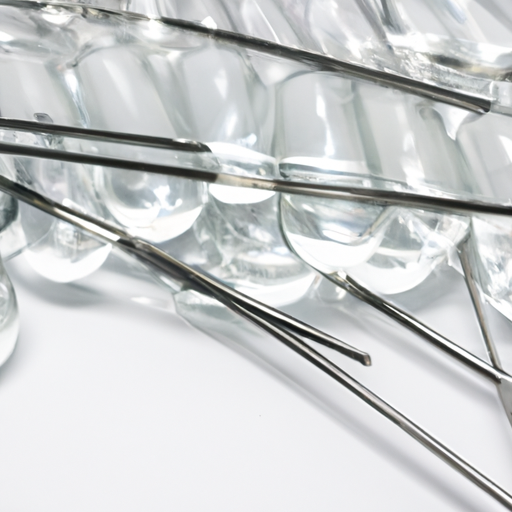
I. Introduction
In the world of electronics, resistors play a crucial role in controlling the flow of electric current. Among the various types of resistors, glass glaze resistors have gained prominence due to their unique properties and manufacturing processes. These resistors are characterized by a glass coating that provides excellent thermal stability, high resistance to environmental factors, and superior electrical performance. This blog post will delve into the manufacturing processes of the latest glass glaze resistors, exploring their historical context, materials, production techniques, quality control measures, innovations, and applications.
II. Historical Context
The evolution of resistor technology has been marked by significant advancements, from simple wire-wound resistors to more complex and efficient designs. Glass glaze resistors emerged as a response to the need for components that could withstand harsh environmental conditions while maintaining reliable performance. Unlike traditional carbon or metal film resistors, glass glaze resistors offer enhanced durability and stability, making them suitable for a wide range of applications. Their introduction marked a pivotal moment in resistor technology, providing engineers with a robust solution for demanding electronic circuits.
III. Materials Used in Glass Glaze Resistors
The performance of glass glaze resistors is heavily influenced by the materials used in their construction.
A. Composition of Glass Glaze
1. **Silica**: The primary component of glass glaze is silica, which forms the glass matrix. Silica provides the necessary thermal and electrical insulation properties.
2. **Fluxing Agents**: These materials lower the melting point of silica, facilitating the formation of a smooth and uniform glass layer. Common fluxing agents include boron oxide and sodium oxide.
3. **Colorants and Additives**: To achieve specific electrical characteristics and aesthetic qualities, various colorants and additives are incorporated into the glass glaze. These can enhance the visibility of the resistor's markings and improve its performance.
B. Conductive Materials
1. **Metal Oxides**: Metal oxides, such as tin oxide and indium oxide, are often used as the primary conductive materials in glass glaze resistors. They provide the necessary resistance values and stability.
2. **Carbon-Based Materials**: In some cases, carbon-based materials are added to improve conductivity and reduce the temperature coefficient of resistance.
C. Substrates
1. **Ceramic Bases**: The substrate for glass glaze resistors is typically made from ceramic materials, which offer excellent thermal stability and electrical insulation.
2. **Other Supporting Materials**: Depending on the application, other materials may be used to enhance the mechanical properties of the resistor.
IV. Manufacturing Processes
The manufacturing of glass glaze resistors involves several intricate processes, each contributing to the final product's quality and performance.
A. Preparation of Raw Materials
1. **Sourcing and Quality Control**: The first step in manufacturing glass glaze resistors is sourcing high-quality raw materials. Rigorous quality control measures are implemented to ensure that all materials meet industry standards.
2. **Mixing and Grinding**: The raw materials are then mixed and ground to achieve a uniform particle size. This step is crucial for ensuring consistent performance in the final product.
B. Forming the Resistor Body
1. **Molding Techniques**: The resistor body is formed using various molding techniques, such as pressing or casting. These methods allow for precise shaping of the resistor to meet specific design requirements.
2. **Extrusion Processes**: In some cases, extrusion processes are employed to create long, continuous shapes that can be cut to the desired length later.
C. Application of Glass Glaze
1. **Coating Techniques**: The application of glass glaze is a critical step in the manufacturing process. Several techniques can be used, including:
- **Dip Coating**: The resistor body is dipped into a molten glass glaze, allowing for a uniform coating.
- **Spray Coating**: A spray method can be used to apply a fine layer of glass glaze, ensuring even coverage.
- **Screen Printing**: This technique allows for precise application of the glass glaze in specific patterns or designs.
2. **Drying and Curing**: After the glaze is applied, the resistors undergo a drying and curing process to solidify the glass coating. This step is essential for achieving the desired mechanical and electrical properties.
D. Sintering Process
1. **Temperature Control**: The sintering process involves heating the coated resistors to a specific temperature, allowing the glass to fuse and bond with the substrate. Precise temperature control is critical to avoid damaging the resistor.
2. **Time Management**: The duration of the sintering process is also carefully managed to ensure optimal performance. Too short a time may result in incomplete bonding, while too long can lead to degradation of the materials.
E. Electrical Termination
1. **Attachment of Leads**: Once the resistors are sintered, electrical leads are attached to facilitate connection in electronic circuits. This step is crucial for ensuring reliable electrical performance.
2. **Soldering Techniques**: Various soldering techniques are employed to secure the leads, ensuring a strong and conductive connection.
V. Quality Control Measures
Quality control is paramount in the manufacturing of glass glaze resistors to ensure they meet the required specifications.
A. Testing for Electrical Properties
1. **Resistance Measurement**: Each resistor is tested for its resistance value to ensure it falls within the specified tolerance range.
2. **Tolerance Testing**: Tolerance testing is conducted to verify that the resistors can perform reliably under varying conditions.
B. Physical Inspection
1. **Visual Checks**: A thorough visual inspection is performed to identify any defects in the glass coating or resistor body.
2. **Dimensional Accuracy**: The dimensions of the resistors are measured to ensure they meet design specifications.
C. Environmental Testing
1. **Thermal Cycling**: Resistors undergo thermal cycling tests to evaluate their performance under extreme temperature variations.
2. **Humidity Resistance**: Humidity resistance tests are conducted to ensure that the resistors can withstand moisture without degradation.
VI. Innovations in Glass Glaze Resistor Manufacturing
The manufacturing processes for glass glaze resistors have seen significant innovations in recent years.
A. Advances in Material Science
New materials and formulations are being developed to enhance the performance and reliability of glass glaze resistors. These advancements contribute to improved thermal stability and reduced size.
B. Automation and Robotics in Production
The integration of automation and robotics in the manufacturing process has increased efficiency and precision. Automated systems can perform repetitive tasks with high accuracy, reducing the risk of human error.
C. Eco-Friendly Manufacturing Practices
As sustainability becomes a priority in manufacturing, eco-friendly practices are being adopted. This includes the use of recyclable materials and processes that minimize waste and energy consumption.
VII. Applications of Glass Glaze Resistors
Glass glaze resistors are utilized in a wide range of applications due to their unique properties.
A. Use in Consumer Electronics
These resistors are commonly found in consumer electronics, such as televisions, smartphones, and computers, where reliability and performance are critical.
B. Industrial Applications
In industrial settings, glass glaze resistors are used in machinery and equipment that require robust components capable of withstanding harsh conditions.
C. Automotive and Aerospace Industries
The automotive and aerospace industries rely on glass glaze resistors for their durability and performance in demanding environments, such as high temperatures and vibrations.
VIII. Conclusion
In summary, the manufacturing processes of glass glaze resistors involve a complex interplay of materials, techniques, and quality control measures. As technology continues to advance, the future of glass glaze resistor manufacturing looks promising, with innovations in material science, automation, and eco-friendly practices paving the way for enhanced performance and sustainability. The importance of continued innovation in this field cannot be overstated, as it ensures that electronic components remain reliable and efficient in an ever-evolving technological landscape.
IX. References
A comprehensive list of academic journals, industry reports, and manufacturer specifications would be included here to support the information presented in this blog post.