What are the Product Standards for Resistor Packaging?
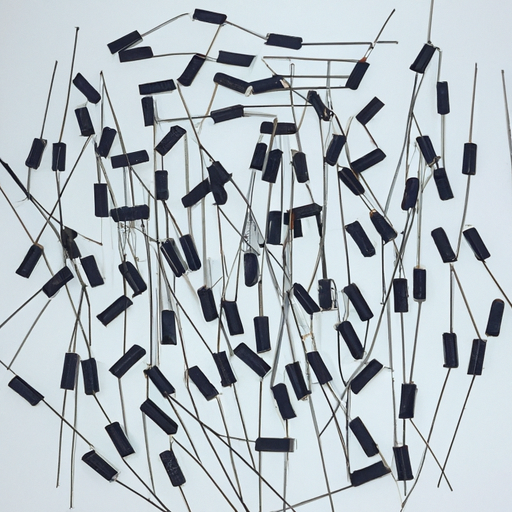
I. Introduction
Resistors are fundamental components in electronic circuits, serving the critical function of controlling current flow and voltage levels. Their importance cannot be overstated, as they are integral to the operation of virtually all electronic devices, from simple household appliances to complex computing systems. However, the performance and reliability of resistors are not solely determined by their electrical properties; the packaging in which they are housed plays a significant role as well. This article aims to explore the product standards governing resistor packaging, shedding light on how these standards ensure the performance, reliability, and safety of resistors in various applications.
II. Understanding Resistor Packaging
A. Types of Resistor Packaging
Resistors come in various packaging types, each suited for different applications and manufacturing processes:
1. **Through-hole Resistors**: These resistors are designed for insertion into a printed circuit board (PCB) through pre-drilled holes. They are typically larger and easier to handle, making them suitable for prototyping and applications where durability is essential.
2. **Surface-mount Resistors**: These resistors are mounted directly onto the surface of a PCB, allowing for more compact designs and higher component density. They are widely used in modern electronics due to their efficiency in automated assembly processes.
3. **Chip Resistors**: A subtype of surface-mount resistors, chip resistors are small, rectangular components that are ideal for high-density applications. Their compact size allows for significant space savings on PCBs.
B. Importance of Packaging in Electrical Performance
The packaging of resistors is crucial for several reasons:
1. **Thermal Management**: Resistors generate heat during operation, and effective packaging helps dissipate this heat, preventing damage and ensuring stable performance.
2. **Mechanical Stability**: The packaging must provide adequate support to resistors, protecting them from mechanical stress and vibration that could lead to failure.
3. **Environmental Protection**: Resistor packaging shields components from environmental factors such as moisture, dust, and chemicals, which can adversely affect performance and longevity.
III. Key Standards Governing Resistor Packaging
A. International Electrotechnical Commission (IEC) Standards
The IEC is a global organization that develops and publishes international standards for electrical and electronic technologies. Several IEC standards are relevant to resistors, including:
1. **IEC 60115**: This standard outlines the general requirements for fixed resistors, including specifications for packaging and testing.
2. **IEC 60068**: This series of standards addresses environmental testing, ensuring that resistors can withstand various conditions such as temperature, humidity, and mechanical stress.
B. Institute of Electrical and Electronics Engineers (IEEE) Standards
The IEEE plays a vital role in establishing standards for electronic components, including resistors. Relevant IEEE standards include:
1. **IEEE 1620**: This standard provides guidelines for the reliability of passive electronic components, including resistors, emphasizing the importance of packaging in maintaining performance.
2. **IEEE 1149.1**: While primarily focused on testing methodologies, this standard also addresses the implications of packaging on the testability of electronic components.
C. Joint Electron Device Engineering Council (JEDEC) Standards
JEDEC is a global leader in developing open standards for the microelectronics industry. Key JEDEC standards for resistor packaging include:
1. **JESD22**: This series of standards covers various testing methods for electronic components, including thermal and mechanical testing relevant to resistor packaging.
2. **JESD51**: This standard focuses on thermal characterization, providing guidelines for measuring the thermal performance of packaged components.
D. American National Standards Institute (ANSI) Standards
ANSI oversees the development of voluntary consensus standards for various industries, including electronics. Relevant ANSI standards for resistors include:
1. **ANSI/IEEE 100**: This standard provides definitions and terminology for electrical and electronic components, including resistors, ensuring clarity in specifications and packaging.
2. **ANSI/IPC-A-610**: This standard outlines acceptability criteria for electronic assemblies, including guidelines for the proper packaging and handling of resistors.
IV. Material Considerations in Resistor Packaging
A. Common Materials Used in Resistor Packaging
The choice of materials for resistor packaging significantly impacts performance and compliance with standards. Common materials include:
1. **Epoxy Resins**: These materials are widely used for their excellent adhesive properties and resistance to environmental factors. They provide a robust protective layer for resistors.
2. **Ceramic Materials**: Ceramic packaging offers superior thermal stability and electrical insulation, making it ideal for high-performance applications.
3. **Metal and Metal Alloys**: Metals are often used for their durability and thermal conductivity, providing effective heat dissipation for resistors.
B. Impact of Material Choice on Performance and Compliance with Standards
The selection of packaging materials directly influences the electrical performance, thermal management, and mechanical stability of resistors. Compliance with industry standards often requires specific material properties, such as resistance to moisture and temperature fluctuations.
C. Environmental Considerations and Regulations
With increasing awareness of environmental issues, regulations such as RoHS (Restriction of Hazardous Substances) and REACH (Registration, Evaluation, Authorisation, and Restriction of Chemicals) have been established. These regulations govern the materials used in resistor packaging, ensuring that harmful substances are minimized or eliminated.
V. Testing and Quality Assurance
A. Importance of Testing in Ensuring Compliance with Standards
Testing is essential to verify that resistor packaging meets established standards. It ensures that components can withstand the rigors of their intended applications and maintain performance over time.
B. Common Testing Methods for Resistor Packaging
1. **Mechanical Testing**: This includes tests for tensile strength, impact resistance, and vibration, ensuring that the packaging can withstand physical stresses.
2. **Thermal Testing**: Thermal cycling and thermal shock tests assess the ability of resistor packaging to handle temperature variations without failure.
3. **Electrical Testing**: This involves measuring resistance values, tolerance levels, and performance under various electrical conditions to ensure compliance with specifications.
C. Quality Assurance Processes in Manufacturing
Manufacturers implement rigorous quality assurance processes to ensure that resistor packaging meets industry standards. This includes regular inspections, testing protocols, and adherence to best practices throughout the production process.
VI. Industry Trends and Innovations
A. Emerging Technologies in Resistor Packaging
1. **Miniaturization**: As electronic devices become smaller and more compact, the demand for miniaturized resistors has increased. This trend necessitates the development of new packaging standards to accommodate smaller sizes while maintaining performance.
2. **Advanced Materials**: Innovations in materials science are leading to the development of new packaging materials that offer improved thermal management, mechanical stability, and environmental protection.
B. Future Directions in Resistor Packaging Standards
1. **Sustainability and Eco-Friendly Practices**: The electronics industry is increasingly focused on sustainability, prompting the development of packaging standards that prioritize environmentally friendly materials and processes.
2. **Adaptation to New Electronic Applications**: As new technologies such as the Internet of Things (IoT) and automotive electronics emerge, resistor packaging standards will need to evolve to meet the unique requirements of these applications.
VII. Conclusion
In conclusion, product standards for resistor packaging are essential for ensuring the reliability and performance of resistors in electronic circuits. These standards, established by organizations such as IEC, IEEE, JEDEC, and ANSI, provide a framework for manufacturers to follow, ensuring that resistors can withstand the demands of their applications. As the electronics industry continues to evolve, so too will the standards governing resistor packaging, with a focus on sustainability, miniaturization, and advanced materials. The future of resistor packaging standards will undoubtedly have a significant impact on the performance and reliability of electronic devices, shaping the way we interact with technology in our daily lives.
VIII. References
1. International Electrotechnical Commission (IEC) - [IEC Standards](https://www.iec.ch)
2. Institute of Electrical and Electronics Engineers (IEEE) - [IEEE Standards](https://www.ieee.org)
3. Joint Electron Device Engineering Council (JEDEC) - [JEDEC Standards](https://www.jedec.org)
4. American National Standards Institute (ANSI) - [ANSI Standards](https://www.ansi.org)
5. RoHS Directive - [RoHS Information](https://ec.europa.eu/environment/waste/rohs_eee/index_en.htm)
6. REACH Regulation - [REACH Information](https://echa.europa.eu/regulations/reach)
What are the Product Standards for Resistor Packaging?
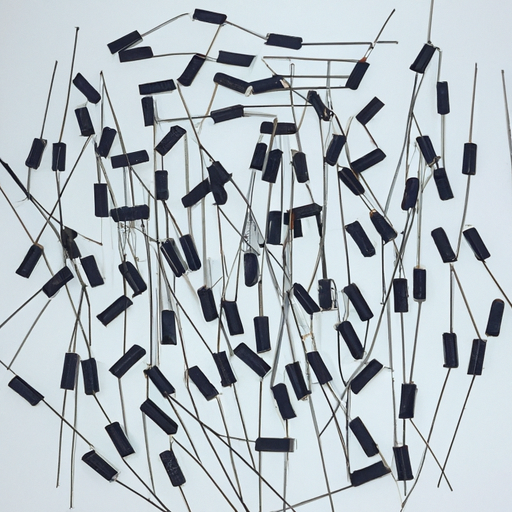
I. Introduction
Resistors are fundamental components in electronic circuits, serving the critical function of controlling current flow and voltage levels. Their importance cannot be overstated, as they are integral to the operation of virtually all electronic devices, from simple household appliances to complex computing systems. However, the performance and reliability of resistors are not solely determined by their electrical properties; the packaging in which they are housed plays a significant role as well. This article aims to explore the product standards governing resistor packaging, shedding light on how these standards ensure the performance, reliability, and safety of resistors in various applications.
II. Understanding Resistor Packaging
A. Types of Resistor Packaging
Resistors come in various packaging types, each suited for different applications and manufacturing processes:
1. **Through-hole Resistors**: These resistors are designed for insertion into a printed circuit board (PCB) through pre-drilled holes. They are typically larger and easier to handle, making them suitable for prototyping and applications where durability is essential.
2. **Surface-mount Resistors**: These resistors are mounted directly onto the surface of a PCB, allowing for more compact designs and higher component density. They are widely used in modern electronics due to their efficiency in automated assembly processes.
3. **Chip Resistors**: A subtype of surface-mount resistors, chip resistors are small, rectangular components that are ideal for high-density applications. Their compact size allows for significant space savings on PCBs.
B. Importance of Packaging in Electrical Performance
The packaging of resistors is crucial for several reasons:
1. **Thermal Management**: Resistors generate heat during operation, and effective packaging helps dissipate this heat, preventing damage and ensuring stable performance.
2. **Mechanical Stability**: The packaging must provide adequate support to resistors, protecting them from mechanical stress and vibration that could lead to failure.
3. **Environmental Protection**: Resistor packaging shields components from environmental factors such as moisture, dust, and chemicals, which can adversely affect performance and longevity.
III. Key Standards Governing Resistor Packaging
A. International Electrotechnical Commission (IEC) Standards
The IEC is a global organization that develops and publishes international standards for electrical and electronic technologies. Several IEC standards are relevant to resistors, including:
1. **IEC 60115**: This standard outlines the general requirements for fixed resistors, including specifications for packaging and testing.
2. **IEC 60068**: This series of standards addresses environmental testing, ensuring that resistors can withstand various conditions such as temperature, humidity, and mechanical stress.
B. Institute of Electrical and Electronics Engineers (IEEE) Standards
The IEEE plays a vital role in establishing standards for electronic components, including resistors. Relevant IEEE standards include:
1. **IEEE 1620**: This standard provides guidelines for the reliability of passive electronic components, including resistors, emphasizing the importance of packaging in maintaining performance.
2. **IEEE 1149.1**: While primarily focused on testing methodologies, this standard also addresses the implications of packaging on the testability of electronic components.
C. Joint Electron Device Engineering Council (JEDEC) Standards
JEDEC is a global leader in developing open standards for the microelectronics industry. Key JEDEC standards for resistor packaging include:
1. **JESD22**: This series of standards covers various testing methods for electronic components, including thermal and mechanical testing relevant to resistor packaging.
2. **JESD51**: This standard focuses on thermal characterization, providing guidelines for measuring the thermal performance of packaged components.
D. American National Standards Institute (ANSI) Standards
ANSI oversees the development of voluntary consensus standards for various industries, including electronics. Relevant ANSI standards for resistors include:
1. **ANSI/IEEE 100**: This standard provides definitions and terminology for electrical and electronic components, including resistors, ensuring clarity in specifications and packaging.
2. **ANSI/IPC-A-610**: This standard outlines acceptability criteria for electronic assemblies, including guidelines for the proper packaging and handling of resistors.
IV. Material Considerations in Resistor Packaging
A. Common Materials Used in Resistor Packaging
The choice of materials for resistor packaging significantly impacts performance and compliance with standards. Common materials include:
1. **Epoxy Resins**: These materials are widely used for their excellent adhesive properties and resistance to environmental factors. They provide a robust protective layer for resistors.
2. **Ceramic Materials**: Ceramic packaging offers superior thermal stability and electrical insulation, making it ideal for high-performance applications.
3. **Metal and Metal Alloys**: Metals are often used for their durability and thermal conductivity, providing effective heat dissipation for resistors.
B. Impact of Material Choice on Performance and Compliance with Standards
The selection of packaging materials directly influences the electrical performance, thermal management, and mechanical stability of resistors. Compliance with industry standards often requires specific material properties, such as resistance to moisture and temperature fluctuations.
C. Environmental Considerations and Regulations
With increasing awareness of environmental issues, regulations such as RoHS (Restriction of Hazardous Substances) and REACH (Registration, Evaluation, Authorisation, and Restriction of Chemicals) have been established. These regulations govern the materials used in resistor packaging, ensuring that harmful substances are minimized or eliminated.
V. Testing and Quality Assurance
A. Importance of Testing in Ensuring Compliance with Standards
Testing is essential to verify that resistor packaging meets established standards. It ensures that components can withstand the rigors of their intended applications and maintain performance over time.
B. Common Testing Methods for Resistor Packaging
1. **Mechanical Testing**: This includes tests for tensile strength, impact resistance, and vibration, ensuring that the packaging can withstand physical stresses.
2. **Thermal Testing**: Thermal cycling and thermal shock tests assess the ability of resistor packaging to handle temperature variations without failure.
3. **Electrical Testing**: This involves measuring resistance values, tolerance levels, and performance under various electrical conditions to ensure compliance with specifications.
C. Quality Assurance Processes in Manufacturing
Manufacturers implement rigorous quality assurance processes to ensure that resistor packaging meets industry standards. This includes regular inspections, testing protocols, and adherence to best practices throughout the production process.
VI. Industry Trends and Innovations
A. Emerging Technologies in Resistor Packaging
1. **Miniaturization**: As electronic devices become smaller and more compact, the demand for miniaturized resistors has increased. This trend necessitates the development of new packaging standards to accommodate smaller sizes while maintaining performance.
2. **Advanced Materials**: Innovations in materials science are leading to the development of new packaging materials that offer improved thermal management, mechanical stability, and environmental protection.
B. Future Directions in Resistor Packaging Standards
1. **Sustainability and Eco-Friendly Practices**: The electronics industry is increasingly focused on sustainability, prompting the development of packaging standards that prioritize environmentally friendly materials and processes.
2. **Adaptation to New Electronic Applications**: As new technologies such as the Internet of Things (IoT) and automotive electronics emerge, resistor packaging standards will need to evolve to meet the unique requirements of these applications.
VII. Conclusion
In conclusion, product standards for resistor packaging are essential for ensuring the reliability and performance of resistors in electronic circuits. These standards, established by organizations such as IEC, IEEE, JEDEC, and ANSI, provide a framework for manufacturers to follow, ensuring that resistors can withstand the demands of their applications. As the electronics industry continues to evolve, so too will the standards governing resistor packaging, with a focus on sustainability, miniaturization, and advanced materials. The future of resistor packaging standards will undoubtedly have a significant impact on the performance and reliability of electronic devices, shaping the way we interact with technology in our daily lives.
VIII. References
1. International Electrotechnical Commission (IEC) - [IEC Standards](https://www.iec.ch)
2. Institute of Electrical and Electronics Engineers (IEEE) - [IEEE Standards](https://www.ieee.org)
3. Joint Electron Device Engineering Council (JEDEC) - [JEDEC Standards](https://www.jedec.org)
4. American National Standards Institute (ANSI) - [ANSI Standards](https://www.ansi.org)
5. RoHS Directive - [RoHS Information](https://ec.europa.eu/environment/waste/rohs_eee/index_en.htm)
6. REACH Regulation - [REACH Information](https://echa.europa.eu/regulations/reach)