What is the Mainstream Production Process of Lifting Resistors?
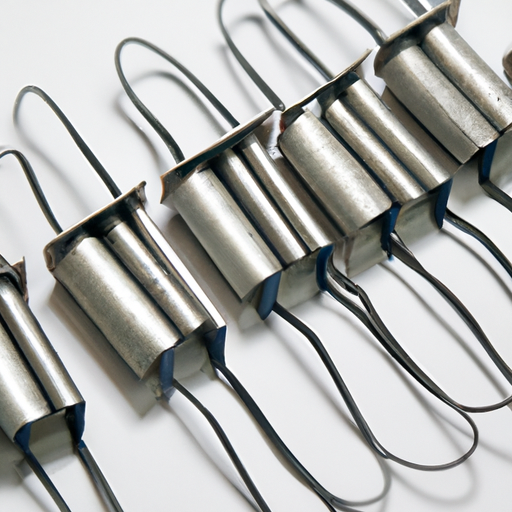
I. Introduction
Lifting resistors are essential components in electronic circuits, playing a crucial role in ensuring signal integrity and proper biasing. These resistors help maintain a defined voltage level in various applications, making them indispensable in modern electronics. This blog post will explore the mainstream production process of lifting resistors, detailing the materials used, manufacturing steps, innovations, challenges, and future trends in the industry.
II. Understanding Lifting Resistors
A. Function and Application of Lifting Resistors
Lifting resistors serve multiple functions in electronic circuits. Primarily, they are used for biasing, which involves setting a specific voltage level to ensure that transistors and other components operate within their optimal range. This is particularly important in analog circuits, where signal integrity is paramount. Lifting resistors are commonly found in various electronic devices, including amplifiers, microcontrollers, and digital signal processors.
B. Types of Lifting Resistors
Lifting resistors can be categorized into three main types:
1. **Fixed Resistors**: These resistors have a predetermined resistance value and are widely used in applications where a stable voltage is required.
2. **Variable Resistors**: Also known as potentiometers, these resistors allow for adjustable resistance values, making them suitable for applications requiring fine-tuning of voltage levels.
3. **Specialty Resistors**: This category includes resistors designed for specific applications, such as high-power or high-frequency environments, where standard resistors may not perform adequately.
III. Raw Materials Used in Lifting Resistor Production
The production of lifting resistors involves various raw materials, each contributing to the resistor's performance and reliability.
A. Conductive Materials
1. **Carbon**: Carbon composition resistors are made from a mixture of carbon and a binding agent. They are known for their stability and cost-effectiveness.
2. **Metal Films**: Metal film resistors are created by depositing a thin layer of metal onto a substrate. They offer high precision and low noise, making them ideal for sensitive applications.
3. **Wire-Wound Materials**: These resistors are made by winding a metal wire around a core. They are suitable for high-power applications due to their ability to dissipate heat effectively.
B. Insulating Materials
1. **Ceramic Substrates**: Ceramic materials are commonly used as substrates for resistors due to their excellent insulating properties and thermal stability.
2. **Epoxy Resins**: These resins are used for encapsulating resistors, providing protection against environmental factors and mechanical stress.
C. Other Components
1. **Lead Materials**: Leads are essential for connecting resistors to circuits. They are typically made from copper or other conductive metals.
2. **Protective Coatings**: Coatings are applied to resistors to enhance their durability and resistance to environmental factors such as moisture and temperature fluctuations.
IV. The Production Process of Lifting Resistors
The production process of lifting resistors involves several key steps, from design and engineering to quality control.
A. Design and Engineering
The production process begins with design and engineering, where specifications and requirements are established. Engineers create prototypes and conduct testing to ensure that the resistors meet the desired performance criteria.
B. Material Preparation
Once the design is finalized, the next step is material preparation. This involves sourcing raw materials and conducting quality control checks to ensure they meet industry standards. Pre-processing of materials, such as cutting and shaping, is also performed at this stage.
C. Manufacturing Steps
1. **Resistor Element Fabrication**:
- **Carbon Composition**: For carbon resistors, a mixture of carbon and binding agents is formed into a cylindrical shape and then baked to achieve the desired resistance.
- **Metal Film Deposition**: In metal film resistors, a thin layer of metal is deposited onto a ceramic substrate using techniques like sputtering or evaporation.
- **Wire-Wound Techniques**: For wire-wound resistors, a metal wire is wound around a ceramic or plastic core, and the resistance is adjusted by varying the length of the wire.
2. **Assembly**:
- **Mounting on Substrates**: The resistor elements are mounted onto substrates, which may include additional components like capacitors or inductors.
- **Soldering and Connections**: Electrical connections are made using soldering techniques to ensure reliable performance.
3. **Encapsulation**:
- **Coating Processes**: Resistors are coated with protective materials to shield them from environmental factors.
- **Curing and Drying**: The encapsulated resistors undergo curing and drying processes to ensure the coatings adhere properly and provide maximum protection.
D. Quality Control
Quality control is a critical aspect of the production process. Various tests are conducted to ensure that the resistors meet specified resistance values and performance criteria. Environmental and durability testing is also performed to assess the resistors' performance under different conditions. Compliance with industry standards, such as ISO and RoHS, is essential to ensure product reliability and safety.
V. Innovations in Lifting Resistor Production
The production of lifting resistors has seen significant innovations in recent years, driven by advancements in materials science and manufacturing technologies.
A. Advances in Materials Science
New materials are being developed to enhance the performance of lifting resistors. For example, the use of nanomaterials can improve the thermal stability and precision of resistors, making them suitable for high-performance applications.
B. Automation and Robotics in Manufacturing
Automation and robotics are increasingly being integrated into the manufacturing process, leading to improved efficiency and consistency. Automated systems can handle repetitive tasks, reducing the risk of human error and increasing production speed.
C. Sustainable Practices and Eco-Friendly Materials
As environmental concerns grow, manufacturers are exploring sustainable practices and eco-friendly materials. This includes using recyclable materials and reducing waste during the production process, contributing to a more sustainable electronics industry.
VI. Challenges in the Production of Lifting Resistors
Despite advancements, the production of lifting resistors faces several challenges.
A. Supply Chain Issues
Global supply chain disruptions can impact the availability of raw materials, leading to delays in production and increased costs.
B. Variability in Raw Material Quality
Inconsistent quality of raw materials can affect the performance and reliability of lifting resistors. Manufacturers must implement stringent quality control measures to mitigate this issue.
C. Meeting Evolving Technological Demands
As technology continues to evolve, the demand for more advanced and specialized lifting resistors increases. Manufacturers must adapt to these changing requirements while maintaining quality and cost-effectiveness.
VII. Conclusion
In summary, the production process of lifting resistors is a complex and multifaceted endeavor that involves careful design, material selection, and manufacturing techniques. As technology advances, the industry is likely to see further innovations and improvements in production methods. Lifting resistors remain a vital component in modern electronics, ensuring the reliability and performance of countless devices. As we look to the future, the significance of lifting resistors in electronic circuits will only continue to grow, underscoring the importance of ongoing research and development in this field.
VIII. References
- Academic journals on electronics and materials science
- Industry reports on resistor manufacturing trends
- Manufacturer guidelines and specifications for lifting resistors
This blog post provides a comprehensive overview of the mainstream production process of lifting resistors, highlighting their importance in electronic circuits and the innovations shaping their future.
What is the Mainstream Production Process of Lifting Resistors?
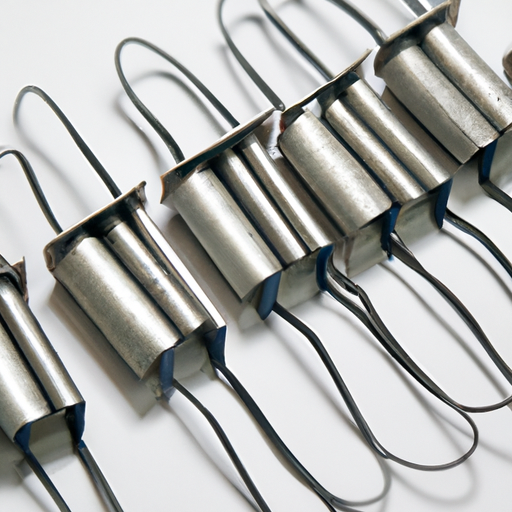
I. Introduction
Lifting resistors are essential components in electronic circuits, playing a crucial role in ensuring signal integrity and proper biasing. These resistors help maintain a defined voltage level in various applications, making them indispensable in modern electronics. This blog post will explore the mainstream production process of lifting resistors, detailing the materials used, manufacturing steps, innovations, challenges, and future trends in the industry.
II. Understanding Lifting Resistors
A. Function and Application of Lifting Resistors
Lifting resistors serve multiple functions in electronic circuits. Primarily, they are used for biasing, which involves setting a specific voltage level to ensure that transistors and other components operate within their optimal range. This is particularly important in analog circuits, where signal integrity is paramount. Lifting resistors are commonly found in various electronic devices, including amplifiers, microcontrollers, and digital signal processors.
B. Types of Lifting Resistors
Lifting resistors can be categorized into three main types:
1. **Fixed Resistors**: These resistors have a predetermined resistance value and are widely used in applications where a stable voltage is required.
2. **Variable Resistors**: Also known as potentiometers, these resistors allow for adjustable resistance values, making them suitable for applications requiring fine-tuning of voltage levels.
3. **Specialty Resistors**: This category includes resistors designed for specific applications, such as high-power or high-frequency environments, where standard resistors may not perform adequately.
III. Raw Materials Used in Lifting Resistor Production
The production of lifting resistors involves various raw materials, each contributing to the resistor's performance and reliability.
A. Conductive Materials
1. **Carbon**: Carbon composition resistors are made from a mixture of carbon and a binding agent. They are known for their stability and cost-effectiveness.
2. **Metal Films**: Metal film resistors are created by depositing a thin layer of metal onto a substrate. They offer high precision and low noise, making them ideal for sensitive applications.
3. **Wire-Wound Materials**: These resistors are made by winding a metal wire around a core. They are suitable for high-power applications due to their ability to dissipate heat effectively.
B. Insulating Materials
1. **Ceramic Substrates**: Ceramic materials are commonly used as substrates for resistors due to their excellent insulating properties and thermal stability.
2. **Epoxy Resins**: These resins are used for encapsulating resistors, providing protection against environmental factors and mechanical stress.
C. Other Components
1. **Lead Materials**: Leads are essential for connecting resistors to circuits. They are typically made from copper or other conductive metals.
2. **Protective Coatings**: Coatings are applied to resistors to enhance their durability and resistance to environmental factors such as moisture and temperature fluctuations.
IV. The Production Process of Lifting Resistors
The production process of lifting resistors involves several key steps, from design and engineering to quality control.
A. Design and Engineering
The production process begins with design and engineering, where specifications and requirements are established. Engineers create prototypes and conduct testing to ensure that the resistors meet the desired performance criteria.
B. Material Preparation
Once the design is finalized, the next step is material preparation. This involves sourcing raw materials and conducting quality control checks to ensure they meet industry standards. Pre-processing of materials, such as cutting and shaping, is also performed at this stage.
C. Manufacturing Steps
1. **Resistor Element Fabrication**:
- **Carbon Composition**: For carbon resistors, a mixture of carbon and binding agents is formed into a cylindrical shape and then baked to achieve the desired resistance.
- **Metal Film Deposition**: In metal film resistors, a thin layer of metal is deposited onto a ceramic substrate using techniques like sputtering or evaporation.
- **Wire-Wound Techniques**: For wire-wound resistors, a metal wire is wound around a ceramic or plastic core, and the resistance is adjusted by varying the length of the wire.
2. **Assembly**:
- **Mounting on Substrates**: The resistor elements are mounted onto substrates, which may include additional components like capacitors or inductors.
- **Soldering and Connections**: Electrical connections are made using soldering techniques to ensure reliable performance.
3. **Encapsulation**:
- **Coating Processes**: Resistors are coated with protective materials to shield them from environmental factors.
- **Curing and Drying**: The encapsulated resistors undergo curing and drying processes to ensure the coatings adhere properly and provide maximum protection.
D. Quality Control
Quality control is a critical aspect of the production process. Various tests are conducted to ensure that the resistors meet specified resistance values and performance criteria. Environmental and durability testing is also performed to assess the resistors' performance under different conditions. Compliance with industry standards, such as ISO and RoHS, is essential to ensure product reliability and safety.
V. Innovations in Lifting Resistor Production
The production of lifting resistors has seen significant innovations in recent years, driven by advancements in materials science and manufacturing technologies.
A. Advances in Materials Science
New materials are being developed to enhance the performance of lifting resistors. For example, the use of nanomaterials can improve the thermal stability and precision of resistors, making them suitable for high-performance applications.
B. Automation and Robotics in Manufacturing
Automation and robotics are increasingly being integrated into the manufacturing process, leading to improved efficiency and consistency. Automated systems can handle repetitive tasks, reducing the risk of human error and increasing production speed.
C. Sustainable Practices and Eco-Friendly Materials
As environmental concerns grow, manufacturers are exploring sustainable practices and eco-friendly materials. This includes using recyclable materials and reducing waste during the production process, contributing to a more sustainable electronics industry.
VI. Challenges in the Production of Lifting Resistors
Despite advancements, the production of lifting resistors faces several challenges.
A. Supply Chain Issues
Global supply chain disruptions can impact the availability of raw materials, leading to delays in production and increased costs.
B. Variability in Raw Material Quality
Inconsistent quality of raw materials can affect the performance and reliability of lifting resistors. Manufacturers must implement stringent quality control measures to mitigate this issue.
C. Meeting Evolving Technological Demands
As technology continues to evolve, the demand for more advanced and specialized lifting resistors increases. Manufacturers must adapt to these changing requirements while maintaining quality and cost-effectiveness.
VII. Conclusion
In summary, the production process of lifting resistors is a complex and multifaceted endeavor that involves careful design, material selection, and manufacturing techniques. As technology advances, the industry is likely to see further innovations and improvements in production methods. Lifting resistors remain a vital component in modern electronics, ensuring the reliability and performance of countless devices. As we look to the future, the significance of lifting resistors in electronic circuits will only continue to grow, underscoring the importance of ongoing research and development in this field.
VIII. References
- Academic journals on electronics and materials science
- Industry reports on resistor manufacturing trends
- Manufacturer guidelines and specifications for lifting resistors
This blog post provides a comprehensive overview of the mainstream production process of lifting resistors, highlighting their importance in electronic circuits and the innovations shaping their future.